welding thin wall steel tubing
2 月 . 15, 2025 08:58

Welding thin wall steel tubing presents unique challenges due to its tendency to warp, burn through, or distort under high heat. However, with the right techniques and understanding, it is possible to achieve precise and strong welds. This article will delve into the intricacies of welding thin wall steel tubing, providing insights based on real-world experiences, technical expertise, and industry best practices.
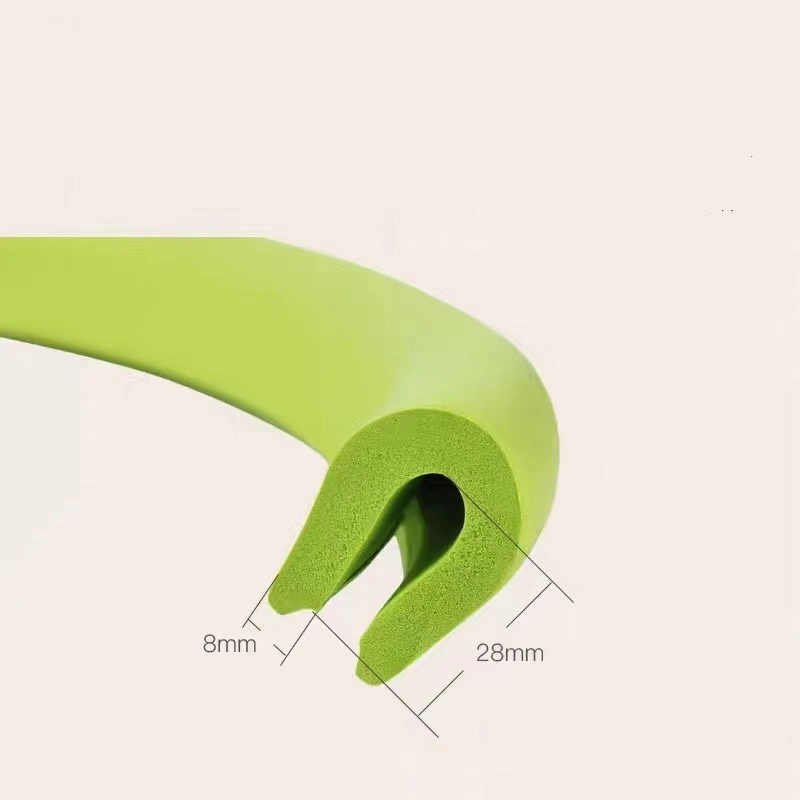
Understanding the Material
Thin wall steel tubing, often used in applications requiring light weight and strength, is typically less than 1/8 inch in thickness. This thinness, while advantageous for applications like bicycle frames, automotive parts, and furniture, requires careful handling during the welding process. The composition of the steel, often mixed with elements like carbon, manganese, or chromium, can affect its response to heat and stress.
Selecting the Right Welding Process
The choice of welding process plays a crucial role in the success of welding thin wall steel tubing. TIG (Tungsten Inert Gas) welding is often the preferred method due to its precision and control, which are paramount in avoiding warping or burn through. MIG (Metal Inert Gas) welding can also be used if adjustments are made to the voltage and wire feed speed to accommodate the thin material.
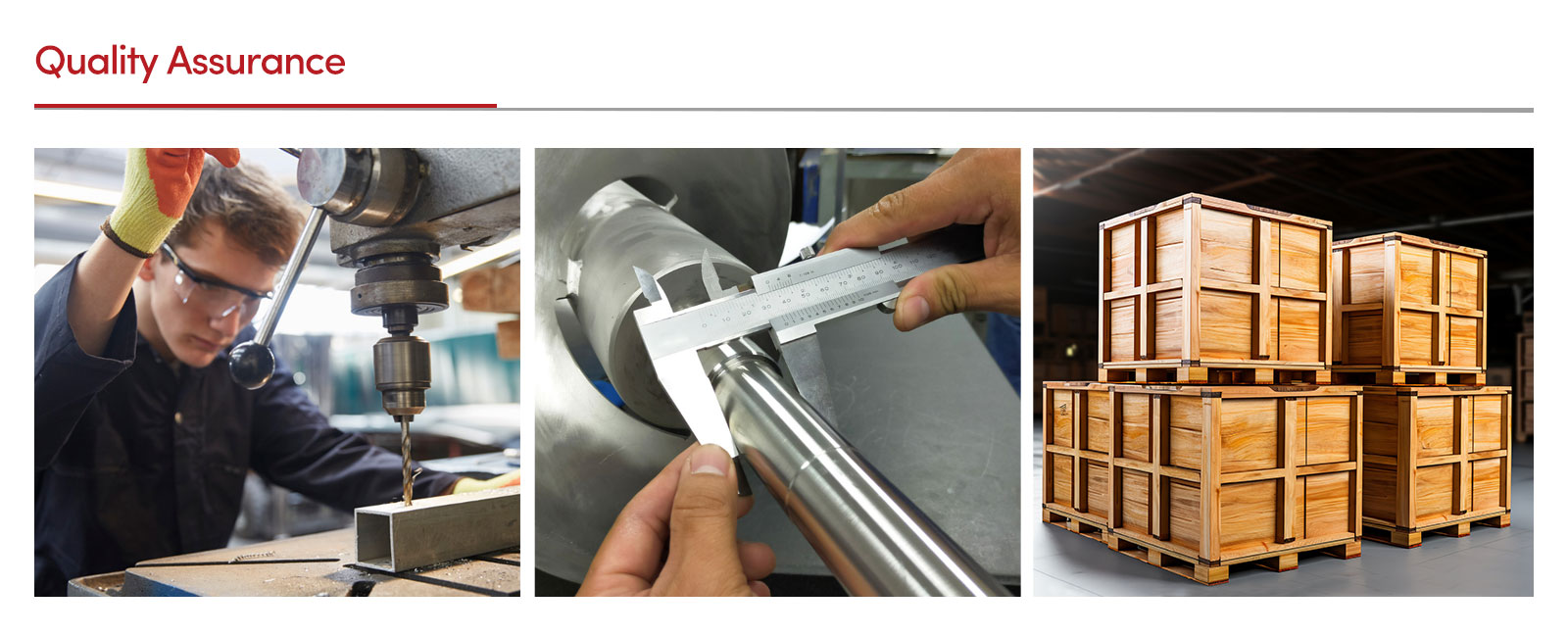
Real-World Experience
Professionals emphasize starting with a clean surface to prevent contaminants from weakening the weld. Using a wire brush or grinder ensures that the surface of the steel tubing is free from rust, paint, or oil. Additionally, clamping the tubing securely prevents movement during the welding process, greatly decreasing the risk of distortion.
The Technique
When welding thin wall tubing, maintaining a steady hand is crucial for producing uniform welds. Experts recommend using pulse welding techniques, which allow the material to cool slightly between heat applications, thus minimizing the risk of burn through. Small tack welds at intervals can also help to hold the tubing in place before completing the full welds, reducing the potential for warping.
Setting the Parameters
Choosing the correct welding parameters is essential. For TIG welding, using a smaller diameter tungsten electrode allows for greater control. Current settings should be adjusted to a lower amp range due to the material's thinness. Similarly, if using MIG welding, reducing the voltage and selecting a lower wire speed helps to prevent burn through.
welding thin wall steel tubing
Safety Considerations
Safety is a top priority when welding. Thin wall tubes can heat up quickly, posing a risk of burns. Proper protective gear, including gloves, a welding helmet, and flame-resistant clothing, is essential.
Testing the Weld
Once completed, the integrity of the weld should be tested. Techniques such as x-ray inspection or ultrasonic testing can detect any weaknesses or inconsistencies. However, a simple visual inspection and a bend test, where a welded section is bent to check for cracking or breakage, can provide a quick assessment of the weld's strength.
Emphasizing Trust
Industry norms suggest documenting each step of the welding process. This documentation serves not only as a record for quality assurance but also builds trust with clients by demonstrating the thoroughness and expertise applied to each project.
Continual Learning
The field of welding is constantly evolving with new technologies and techniques. Keeping abreast of the latest advancements through workshops, certifications, and technical papers is invaluable for maintaining and improving welding proficiency.
Welding thin wall steel tubing demands a harmonious blend of skill, patience, and precision. By understanding the material properties, employing the correct techniques, and adhering to safety protocols, welders can achieve high-quality results. This expertise not only builds a welder's reputation but also assures clients that their projects are in capable, reliable hands.