Trunk Hinges
2 月 . 15, 2025 08:16

Mastering the art of welding thin wall aluminum tubing requires a fusion of precision, skill, and expertise. This process is integral in various industries, from automotive to aerospace, due to aluminum's lightweight and corrosion-resistant properties. However, welding thin-wall aluminum tubing presents unique challenges that demand a keen understanding of the material's characteristics and the nuances of the welding process.

When dealing with aluminum, it's paramount to understand its high thermal conductivity and low melting point. These properties necessitate a delicate balance during welding to avoid warping or burning through the material. Thin wall tubing, especially, requires meticulous attention because its reduced thickness amplifies these challenges. A small misstep can compromise the integrity of the entire structure, making the expertise in technique crucial for success.
Choosing the correct welding technique is crucial. TIG (Tungsten Inert Gas) welding, known for its precision and control, is often the preferred method for thin wall aluminum. TIG welding allows for precise heat control which is critical in avoiding burn-through or warping. The use of a high-frequency start on the TIG welder is advisable, as it helps in initiating the arc without physical contact, reducing contamination risks and ensuring a clean weld.
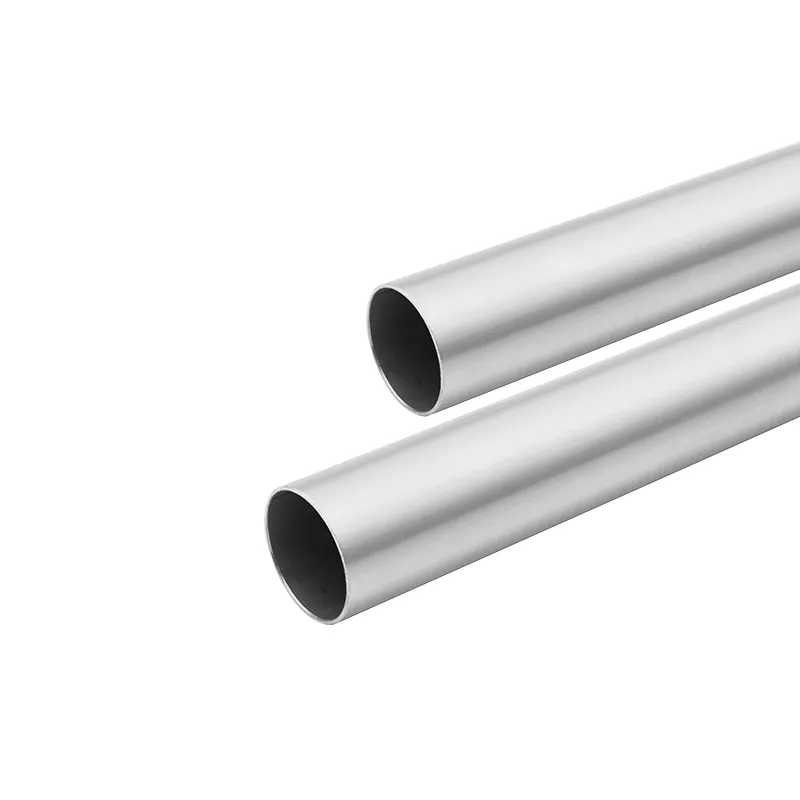
Equally important is the selection of the right filler material. For aluminum, a filler metal that closely matches the composition of the tubes is essential to maintain the aluminum’s inherent properties. Using a mismatch can lead to corrosion or structural weaknesses over time. Generally, 4043 and 5356 are popular filler choices for their versatility and strength when working with aluminum.
Pre-welding preparation cannot be overlooked. Aluminum is notorious for its oxide layer that can prevent proper fusion. Thorough cleaning of the tubing with a non-abrasive brush or chemical cleaner is necessary to remove oxides and any contaminants. Once cleaned, the parts should be assembled and welded promptly to minimize the risk of oxide reforming.
welding thin wall aluminum tubing
The welding environment must also be controlled meticulously. A consistent shielding gas flow, typically Argon, should be maintained to protect the weld pool from atmospheric contamination. The purity of the gas directly influences the quality of the weld; thus, ensuring high purity levels is vital.
Beyond technique and preparation, understanding the nuances of heat management is critical. Thin aluminum can deform under excessive heat, so it’s important to use a back-stepping technique or start from tack welds to distribute heat evenly across the tubing. This approach reduces the risk of overheating any single area.
Post-weld treatment can also enhance results. Techniques like annealing can relieve stresses introduced during welding. This process helps in maintaining the dimensional stability and overall appearance of the structure, making it a crucial step in ensuring long-term durability and performance.
In a world where precision and reliability are paramount,
mastering the welding of thin wall aluminum tubing is an invaluable skill. It elevates the quality of products, from bikes to aircraft, ensuring safety, performance, and longevity. With the right mix of technique, preparation, and material understanding, this complex task becomes an achievable feat, heralding a new standard in manufacturing.
Professionals in industries relying on welded aluminum structures constantly seek innovation and refinement in welding techniques. The knowledge gleaned from years of hands-on experience and continuous learning becomes a cornerstone of authority in this craft. As advancements in technology and materials science introduce new challenges and opportunities, staying informed and skilled remains imperative. Thus, dedication to mastering these techniques not only enhances technical prowess but also fortifies the foundation of trust and reliability that industries heavily depend on.