Special-shaped Tube For Furniture
2 月 . 15, 2025 07:58

Welding thin tubing is an art that demands precision, extensive knowledge, and the right equipment. In industries like aerospace, automotive, and even plumbing, the ability to join thin-walled tubes without compromising structural integrity is crucial. Here's a comprehensive guide that builds on years of expertise and authoritative knowledge, aimed at ensuring effective and reliable results.
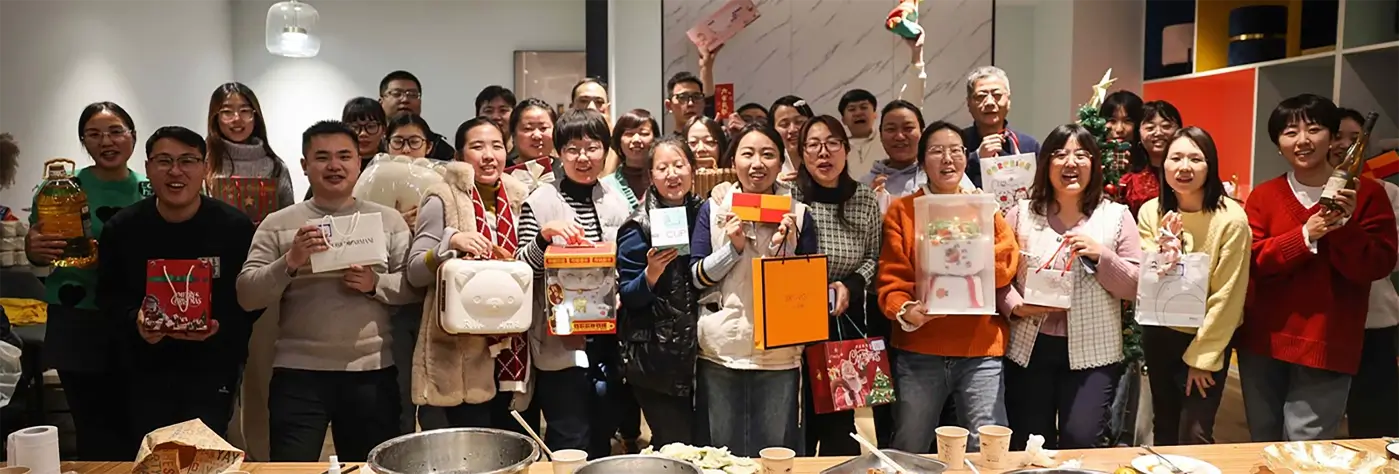
Understanding the Material
The first step in welding thin tubing is thoroughly understanding the material you're working with. Each type of metal presents its unique challenges. For instance, stainless steel, while corrosion-resistant, has a tendency to warp under high heat. Aluminum, on the other hand, dissipates heat rapidly, requiring careful management of thermal cycles. A familiarity with these and other materials is essential to anticipate potential challenges and adjust your technique accordingly.
Choosing the Right Welding Technique
TIG (Tungsten Inert Gas) welding is often the go-to technique for thin tubing due to its precision and control. Unlike MIG (Metal Inert Gas) welding, which can cause burn-through on thin materials, TIG welding allows for greater finesse. The non-consumable tungsten electrode provides a stable arc, essential for maintaining the aesthetics and integrity of welds on thin-walled tubes. Mastery in adjusting amperage and using filler rods appropriately is key to prevent warping and ensure solid welds.

Preparing the Tubing
Before striking an arc, meticulous preparation of the tubing is required. Cleaning the metal surface thoroughly is critical; contaminants can result in imperfections and weak joints. Use a degreaser or a solvent to remove all oils, dirt, or any oxidation. For a snug fit-up,
deburr the ends of your tubing. Misalignment can lead to poor welds or excessive gaps that are challenging to fill on thin materials.
Controlling Heat Input
One of the biggest challenges when welding thin tubing is controlling heat input. Too much heat can cause burn-through, while too little may result in a weak joint. Utilize techniques such as pulse welding, which alternates between high and low current, allowing the metal to cool slightly between pulses. Additionally, implementing heat sinks can absorb excess heat and reduce the risk of warping, thus maintaining the structural integrity of the tubing.
Fixture and Joint Design
Clamping the tubing securely is imperative to prevent movement during welding. Custom fixtures or jigs can help maintain alignment and position. When designing joints, consider using lap joints rather than butt joints whenever possible. Lap joints provide a larger heat sink and more surface area to work with, reducing the risk of burn-through.
welding thin tubing
Monitoring and Adjustment
Welding thin tubing is not a static process; it requires constant monitoring and adjustments. Watch the weld pool closely to ensure it doesn’t get too large or too hot. Adjust the travel speed and filler rod accordingly. Consistent practice and adjustments based on real-time observations can drastically improve weld quality and efficiency.
Post-Weld Inspection and Testing
After welding, inspect the weld seam visually and through non-destructive testing methods like dye penetrant or X-ray inspection to ensure joint integrity. This step is crucial to verify that there are no hidden defects that could lead to failures in critical applications. Professionalism in post-weld processes underscores trustworthiness and confidence in your outcomes.
Safety Considerations
Safety should never be an afterthought in welding. High-frequency currents used in TIG welding, along with the fumes and UV light emitted during the process, require comprehensive safety measures. Proper ventilation, protective eyewear, and clothing are paramount to protect against ultraviolet and infrared rays, which can cause eye and skin damage.
Experience and Continual Improvement
Becoming skilled in welding thin tubing is not a one-time achievement. It requires continual learning and adaptation to new technologies and techniques. Joining professional groups and attending workshops can enhance your expertise and keep you updated with the latest advancements in welding technology, contributing to a robust professional portfolio.
In conclusion, welding thin tubing is a specialized skill that marries knowledge with practical application. It demands an understanding of materials, a mastery of techniques, and an unwavering commitment to quality and safety. By approaching each project with a methodical and informed strategy, welders can produce joints that are not only functional but also exhibit the highest standards of craftsmanship.