Medical Bed Frame
2 月 . 15, 2025 06:20

Welding small aluminum tubing requires both expertise and the right tools, embodying a skill crucial in industries ranging from aerospace to automotive customization. This article delves into the nuances of aluminum tube welding, offering a blend of real-world experience, expert insights, and authoritative guidance to ensure reliable, high-quality welds, solidifying your project's structural integrity.
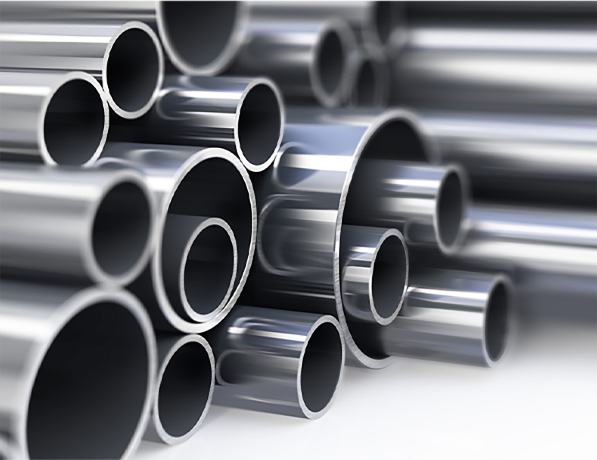
Aluminum's lightweight properties and corrosion resistance make it an attractive choice for various applications. However, its unique thermal conductivity and oxide layer require specific welding techniques. The intricacies involved in such operations necessitate a detailed understanding for optimal results.
Understanding Aluminum's Nature
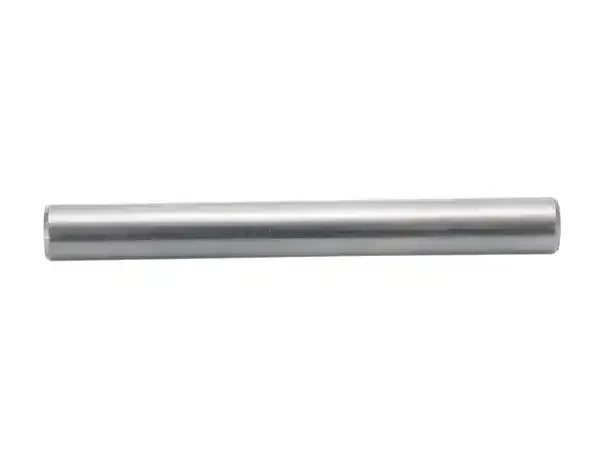
Aluminum is a non-ferrous metal known for its high strength-to-weight ratio and excellent corrosion resistance. However, its high thermal conductivity and melting point present unique challenges. The oxide layer formed on aluminum melts at a much higher temperature than the metal itself, influencing the welding process.
Choosing the Right Welding Method
TIG (Tungsten Inert Gas) welding is widely recommended for small aluminum tubing. Its precise control over the welding arc and use of a non-consumable tungsten electrode make it suitable for detailed work. For beginners and professionals alike, investing in quality TIG welding equipment is crucial. Features like adjustable amperage and AC balance control are essential for managing the heat and cleaning action required for clean aluminum welds.
Preparing the Aluminum Tubing
Proper preparation cannot be overstated. Aluminum should be free from contaminants to ensure a strong weld. Use a stainless steel brush dedicated solely to aluminum to clean surfaces. It's critical to remove the oxide layer immediately before welding. This prevents contamination and facilitates a cleaner, stronger weld.
Setting Up the Work Environment
Mindful setup of the welding environment can significantly enhance weld quality. Ensure a stable power supply and clean, dry conditions. Using clamps to secure the tubing in place will help maintain stability and alignment during welding.
Executing the Weld
welding small aluminum tubing
While welding, maintain a steady hand and consistent pace. Aluminum transfers heat quickly, requiring careful management of the torch to prevent burn-through. Practice makes perfect; beginners might find it beneficial to practice on scrap pieces before tackling project components. Maintain a tight arc length and consistent speed for an even bead. TIG welding requires coordination as you feed the filler rod with one hand while handling the torch in the other.
Expert Insight Avoiding Common Pitfalls
Overheating can cause warping or burn-through. Maintaining appropriate heat levels is crucial – hence, the importance of having a welder with adjustable heat settings. Besides, using inappropriate filler materials can lead to weak joints. Consider using a filler alloy compatible with your aluminum grade, ensuring alignment in terms of strength and corrosion resistance.
Investing in Professional Equipment
In the realm of small aluminum tubing welding, inferior equipment can diminish the quality of your work. Professional-grade TIG welders, though typically more costly, guarantee additional features such as pulse welding capabilities and advanced control settings. Such investments pay off through superior performance and durability.
Quality Assurance
Post-weld inspection is a non-negotiable step. Examine for imperfections such as cracks or porosity, which can compromise the integrity of the joint. Implementing non-destructive testing methods, like dye penetrant inspection, can reveal flaws not visible to the naked eye.
Maintaining Welding Equipment
Keeping your welding gear in top condition ensures reliable performance over time. Regularly inspect cables and consumables like electrodes for wear and tear. Proper maintenance directly translates to consistent weld quality.
Welding small aluminum tubing effectively requires an amalgam of skill, precision, and the right tools. Adopting these strategies not only fosters superior outcomes but also establishes your authority and trustworthiness in the field. By investing in understanding and mastering this craft, the welded products you produce will stand the test of time, serving as a testament to your expertise and commitment to quality.