Cross Car Beam
2 月 . 15, 2025 06:00

Welding scaffold tubes is a crucial process in the construction and industrial sectors, demanding precision, expertise, and a keen understanding of both the materials involved and the safety protocols required. Scaffold tubes, mainly composed of steel or aluminum, serve as the backbone for temporary structures providing access to elevated work areas. The welding process is integral in ensuring these structures are secure and reliable.

Welding Expertise and Techniques for Scaffold Tubes
The choice of welding technique is paramount. MIG (Metal Inert Gas) welding is widely preferred due to its efficiency and strong welds, which are essential in high-stress environments. TIG (Tungsten Inert Gas) welding, although slower, provides more precision and is ideal for aluminum scaffold tubes which require careful handling due to their lower melting point compared to steel.
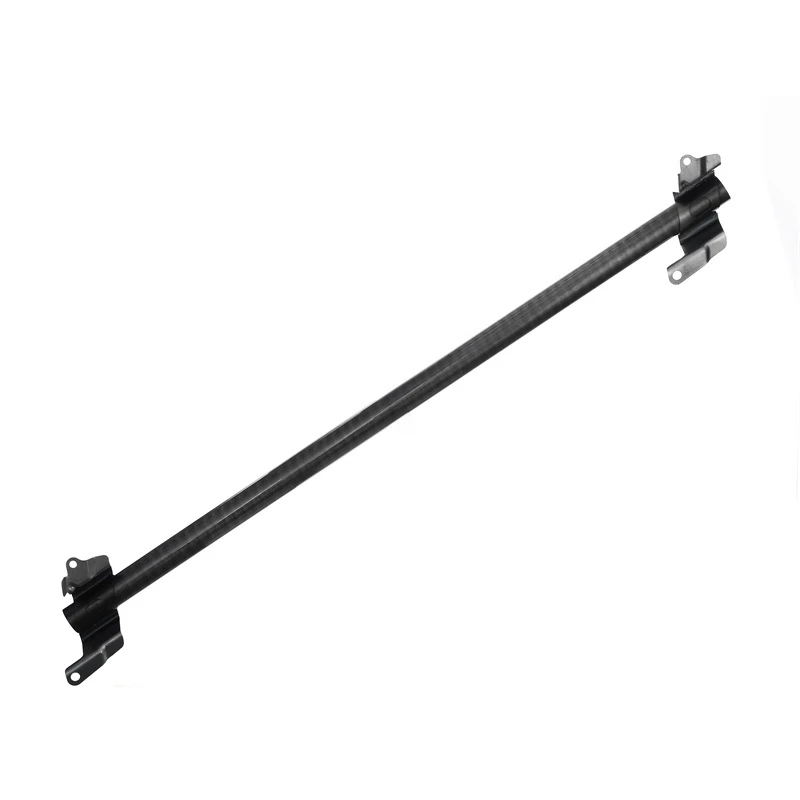
A seasoned welder understands the nuances each material presents. Steel scaffold tubes demand specific attention to stress distribution. Welding must avoid excessive heat exposure which can compromise structural integrity through warping or undue stress concentrators. The thickness of scaffold tubes also dictates the welding parameters; hence, an in-depth understanding of these variables is crucial for optimal results.
Ensuring Authoritativeness and Trustworthiness in Welding Practices
Industries that regularly utilize welded scaffold systems emphasize compliance with recognized standards, such as those set by the American Welding Society (AWS) and the British Standards Institution (BSI). These standards assure that the welding processes, when correctly followed, provide structures capable of withstanding necessary load requirements and environmental conditions.
Certified welding professionals are a must in projects involving scaffold tubes. Certification ensures adherence to best practices and the ability to handle unexpected complexities during the welding process. Firms should only engage welders who have both the credentials and consistent track records of adhering to high-quality welding standards.
Safety A Non-Negotiable Aspect
Safety is non-negotiable in welding scaffold tubes. The inherent risks demand stringent safety protocols. This encompasses wearing appropriate protective gear, like helmets with proper visor standards, gloves, and work boots that minimize the risk of electric shock or heat exposure.
Furthermore, the work environment needs to be meticulously organized. Adequate ventilation systems reduce the inhalation of harmful fumes, while robust grounding mechanisms and regular equipment checks forestall potential malfunctions that might lead to injuries or fatalities.
Building a Reputation on Experience and Quality Assurance
welding scaffold tube
For companies involved in constructing scaffolding systems, building a reputation grounded in experience is essential. Real-world experience in various scenarios — from extreme weather conditions to working in confined spaces — enables professionals to foresee potential challenges and address them proactively.
Quality assurance in welding is realized through systematic inspections and testing. Non-destructive testing (NDT) methods, such as radiographic and ultrasonic testing, are employed to assess the integrity of welds without compromising the structure. These tests confirm that each weld can withstand the anticipated stresses and maintain its integrity over its intended lifespan.
Customer relationships hinge on trust. Detailed documentation of welding records, maintenance logs, and compliance reports form the foundation of transparent operations — boosting client confidence in the reliability of their scaffolding systems.
Continuous Improvement and Learning
The landscape of welding technology is ever-evolving, presenting new tools and techniques that enhance efficiency and safety. Welders committed to excellence must engage in continuous learning, keeping abreast of innovations such as robotic welding and improved welding consumables which enhance the quality and speed of projects.
Additionally, digital technologies like 3D modelling and simulation allow for the pre-assessment of scaffold configurations and stress testing before actual implementation, enabling better planning and execution.
Promoting Sustainable Welding Practices
Sustainability is an increasingly pivotal component of modern welding processes. Employing eco-friendly materials and energy-efficient welding techniques not only reduces environmental impact but also aligns with global efforts towards sustainable construction practices.
Recycling scrap metals effectively and choosing recycled materials for new scaffolding further bolster a company’s commitment to sustainable practices, appealing to environmentally-conscious clients.
In conclusion, mastering the art of welding scaffold tubes goes beyond mere technical ability. It requires a blend of technical know-how, strict adherence to safety and quality standards, and a forward-thinking approach to sustainability. Companies that align their practices with these principles not only secure a competitive edge but also establish themselves as leaders in the construction industry, trusted by partners and clients alike.