HC340/590DP Headrest Shrink Tube
2 月 . 15, 2025 05:41

Welding round tube steel is a critical process in various industries, from automotive to construction. The proficiency in this technique not only ensures structural integrity but also enhances safety and functionality. Here, we delve into the nuances that define the welding of round tube steel, addressing the pivotal aspects that establish it as a reliable practice in the manufacturing sector.
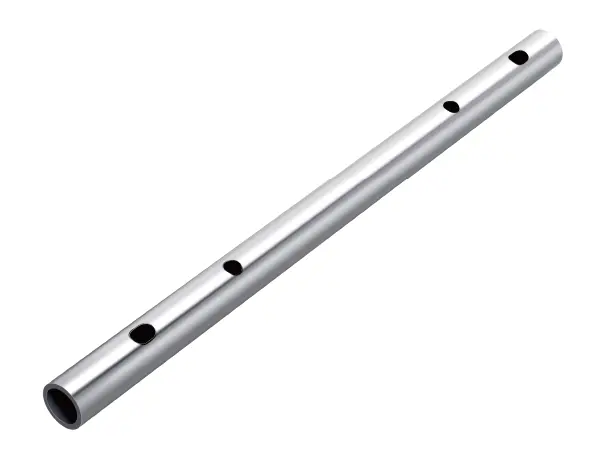
Achieving a perfect weld on round tube steel involves more than just technical know-how; it requires a thorough understanding of material characteristics and welding environments. Round tubes, frequently utilized for their aesthetic and structural advantages, present unique challenges when it comes to welding due to their geometry. The curved surfaces necessitate precise alignment and consistent weld penetration to avoid weak spots that could compromise the structure’s integrity.
Seasoned professionals emphasize the importance of selecting the appropriate welding technique for round tube steel. Techniques such as Tungsten Inert Gas (TIG) and Metal Inert Gas (MIG) welding are preferred for their precision and control. TIG welding, noted for its cleaner welds and minimal spatter, is ideal for applications demanding high-quality aesthetics and strength. MIG welding, on the other hand, offers speed and efficiency, making it a suitable alternative for larger production runs where surface finish is not a critical concern.

Moreover, the choice of filler material plays a crucial role in achieving a successful weld. Industry experts underline the necessity of using a filler material that matches the base metal's composition to prevent corrosion and ensure a strong bond. This extends the longevity of the final product and maintains structural integrity under varying environmental conditions.
The welding environment also influences the outcome significantly. Proper ventilation, humidity control, and a stable work surface are essential to maintain the cleanliness and precision required for welding round tube steel. Impurities in the environment can introduce defects into the weld, leading to potential failures in high-stress applications.
welding round tube steel
Operators must be well-trained and experienced, as the skill level directly impacts the welding quality. An expert welder can adjust parameters on the fly to accommodate variations in tube thickness or composition, ensuring consistent quality across different sections of the tube. This requires a deep understanding of the welding equipment and a keen eye for detail.
Quality control is another dimension crucial to the process of welding round tube steel. Rigorous inspection protocols, such as non-destructive testing and metallurgical analysis, are employed to verify the weld quality. These measures help detect inconsistencies or defects early, allowing for corrective action before the product reaches the end user.
Incorporating automation into welding processes has emerged as a revolutionary trend, enhancing precision and repeatability. Automated systems equipped with advanced sensors and AI technology can monitor weld quality in real-time, reducing the likelihood of human error and ensuring consistent output across production batches.
In summary, welding round tube steel with excellence demands a blend of expertise, meticulous planning, and advanced technology. By adhering to best practices and leveraging modern innovations, manufacturers can produce reliable and robust structures that meet the stringent demands of today’s industrial applications. This commitment to quality not only fosters trust with customers but also positions the manufacturer as a leader in the industry, synonymous with reliability and excellence.