welding rectangular tubing
2 月 . 15, 2025 05:21

Welding rectangular tubing is a fundamental skill for many in the fabrication industry, where the strength and precision of structures are crucial. Understanding the nuances of welding this type of material is essential for ensuring the durability and integrity of the final product. In this article, we delve into the intricacies of welding rectangular tubing, providing insights from experienced professionals and emphasizing the importance of expertise and trustworthiness in this field.
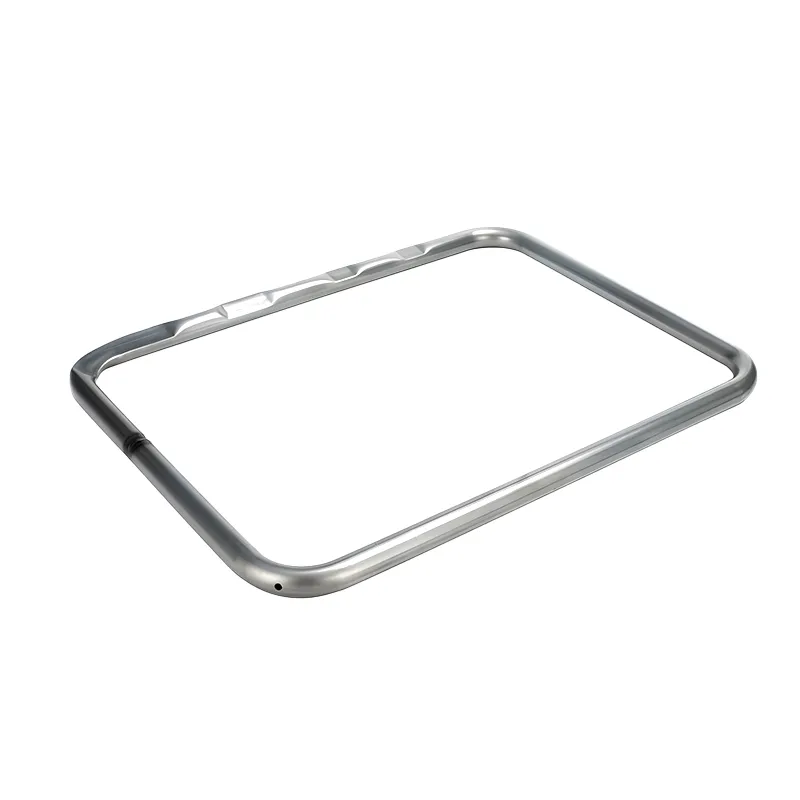
Rectangular tubing, commonly used in frames, metal structures, and various construction applications, requires a specific set of techniques to weld effectively. One crucial aspect of welding rectangular tubing is joint preparation. Ensuring that your joints are clean and properly aligned is the first step in achieving a strong weld. Experienced welders know that any mill scale, rust, or debris must be thoroughly removed to prevent contamination and ensure proper fusion. The use of angle grinders or flap discs is often recommended for cleaning and smoothing the edges.
When it comes to choosing the appropriate welding method,
MIG welding often stands out as a preferred choice for rectangular tubing. MIG welding provides precision and flexibility, allowing welders to create smooth, consistent beads, which is particularly important when working with thinner-walled tubing. The key is to adjust the voltage and wire feed speed appropriately, a task that demands hands-on experience and a deep understanding of the welding process. Professional welders often emphasize the importance of performing test welds on scrap materials to fine-tune these parameters before proceeding to the final project.
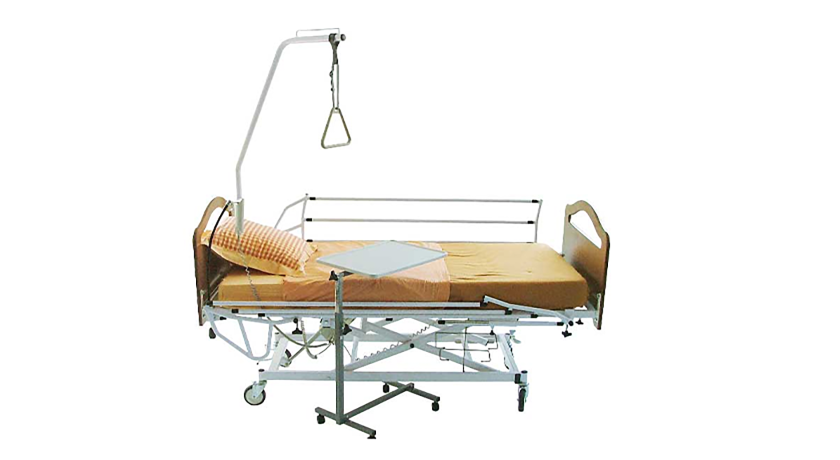
Another essential consideration is the positioning of the tubing during the welding process. Horizontal position is often recommended for beginners, as it provides a stable platform and reduces the complexity associated with vertical or overhead welding. However, seasoned welders with extensive expertise might tackle vertical or even overhead welds when the project demands it. Regardless of the position, using clamps or jigs to secure the tubing is critical for maintaining alignment and reducing movement during welding.
welding rectangular tubing
Moreover, heat management is a significant factor in welding rectangular tubing. Excessive heat can lead to warping or distortion, particularly in thinner-walled tubes. Welders with authoritative knowledge in this domain stress the importance of using intermittent welding techniques, such as stitch welding, to minimize heat buildup. This method not only preserves the integrity of the tubing but also contributes to a more aesthetically pleasing weld.
A vital part of becoming an expert in welding rectangular tubing is continuous learning and adaptation to new technologies and materials. Staying updated with advancements in welding equipment, such as inverter-based power sources, can enhance weld quality and efficiency. Additionally, participating in workshops and certifications helps in refining skills and ensuring that one's knowledge base remains current and trustworthy.
To establish authority in this field, welders should consider contributing to forums, publishing case studies, or mentoring upcoming professionals. Sharing experiences and challenges faced during specific projects provides valuable insights to peers and helps build a reputation for reliability and expertise.
In conclusion, welding rectangular tubing is more than just a technical skill; it is an art that combines precision, knowledge, and continuous learning. By maintaining focus on preparation, technique, and material management, welders can achieve superior results that stand the test of time. The expertise and trustworthiness demonstrated in this craft not only enhance individual credibility but also contribute significantly to the industry's overall standards and practices.