welding metal tubing
2 月 . 15, 2025 05:00

Mastering the art of welding metal tubing is not just a matter of technical skill but an endeavor deeply rooted in expertise and a commitment to quality. In an industry where precision and durability determine success, selecting the appropriate welding technique is paramount. Whether building industrial structures or crafting intricate metal frameworks, understanding the nuances of welding metal tubing can elevate a product from standard to stellar.
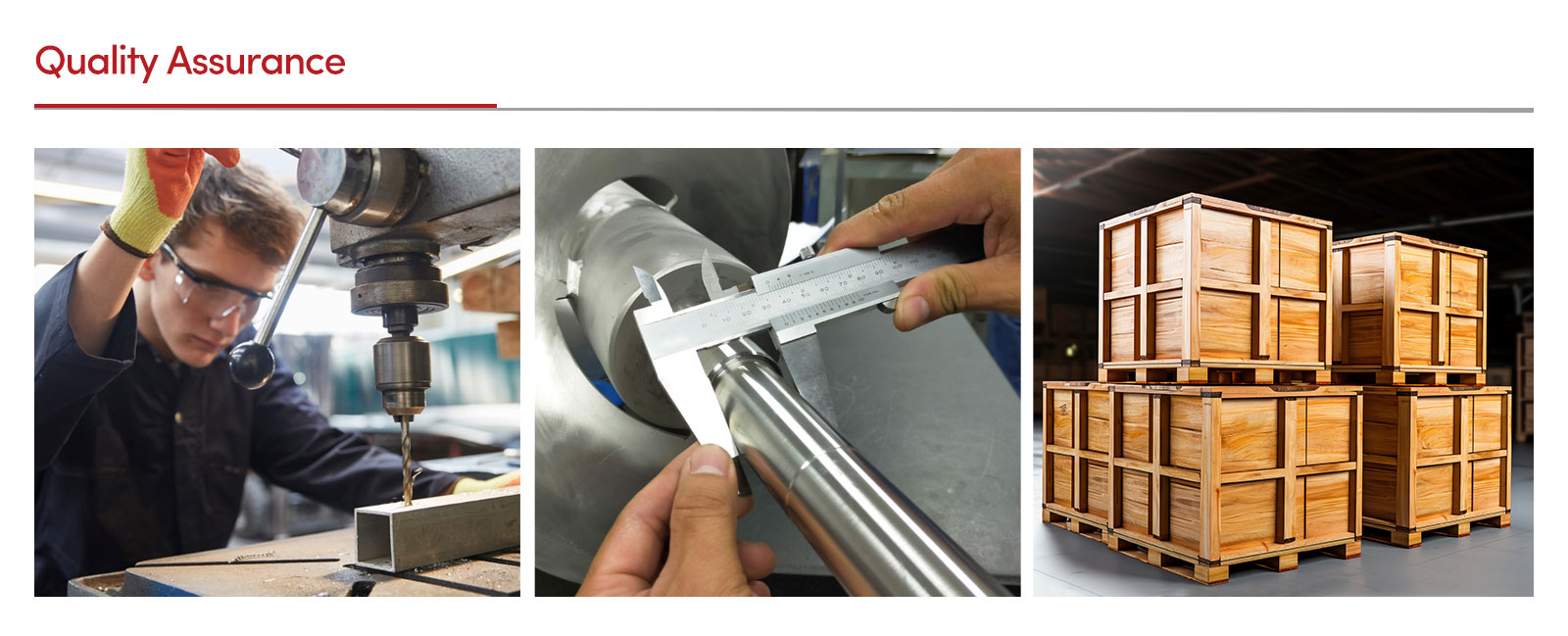
Welding metal tubing involves a variety of methods, each suited to specific applications. One of the most popular techniques is Gas Tungsten Arc Welding (GTAW), more commonly known as TIG welding. This method is renowned for its precision and is the go-to choice for projects where clean, high-quality welds are required. TIG welding's ability to join a wide array of metals, including stainless steel, aluminum, and magnesium, makes it indispensable for diverse industrial applications.
For those seeking efficiency in large-scale production, Gas Metal Arc Welding (GMAW or MIG welding) offers a compelling solution. MIG welding is favored for its speed and adaptability, making it ideal for thicker sections of metal tubing. This method employs a continuously fed wire, which simplifies the welding process and reduces downtime compared to other techniques. Its efficiency makes it a staple in manufacturing environments where time is of the essence, yet structural integrity cannot be compromised.
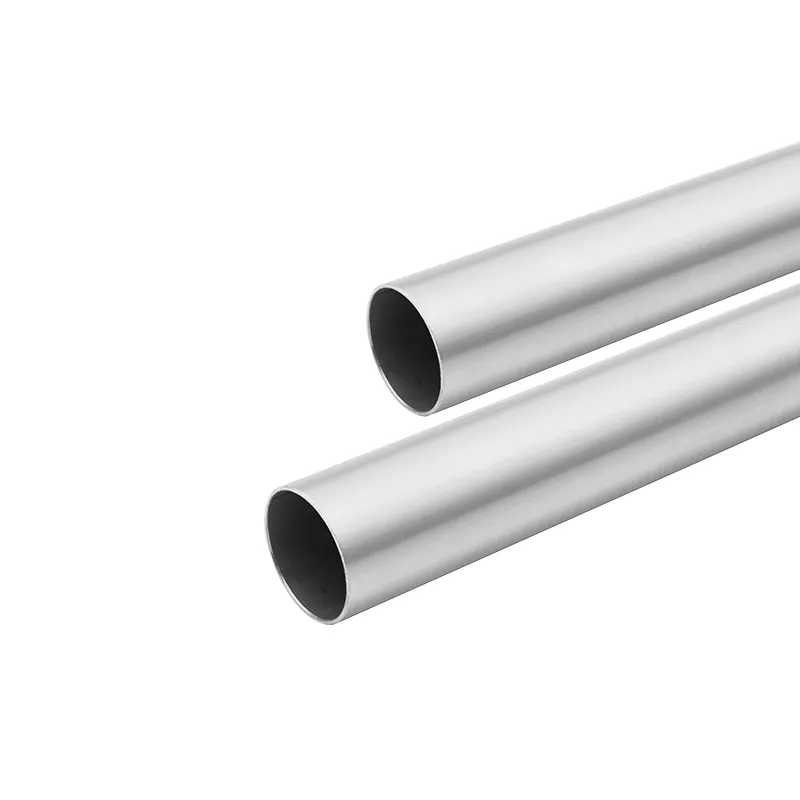
Then there’s the technique of Flux-Cored Arc Welding (FCAW), which provides a unique blend of flexibility and power. With its self-shielding capabilities, FCAW overcomes barriers posed by outdoor environments or conditions that challenge other welding processes. This adaptability ensures a consistent, reliable weld even when environmental factors are less than ideal, making it a preferred choice for construction and shipbuilding industries.
In the automotive and aeronautics industries, resistance spot welding has made a name for itself. Known for its ability to swiftly weld thin metal sheets, this method is crucial for ensuring the lightweight yet robust construction of modern vehicles and aircraft. Its precision and speed significantly contribute to the assembly line production, offering a reliable method for achieving structurally sound joints without sacrificing production efficiency.
welding metal tubing
Understanding these welding techniques' intricacies is only part of crafting flawless metal tubing products. Equally important is the welding environment and preparation of the metal surfaces. Cleanliness is paramount; contaminants such as oils, dust, or rust can compromise the integrity of the weld. Therefore, thorough cleaning of the metal surface using industrial solvents or abrasive cleaning ensures an uncontaminated weld area, critical for achieving a seamless, defect-free bond.
Equipped with the right tools and safety gear, welders must balance heat input to avoid warping or burning through the metal tubing. Mastery of heat control not only preserves the structural integrity of the metal but also produces aesthetically pleasing finishes that meet the highest standards.
Despite the technical challenges, advancements in welding technology continually push the boundaries of what is possible. Laser welding, for instance, is emerging as a sophisticated technique for exceptionally precise and high-speed operations, offering minimal distortion and the ability to weld hard-to-reach areas.
For businesses invested in welding metal tubing, investing in skilled personnel and modern equipment is essential. Training programs that enhance the proficiency of welders and an environment that fosters continuous learning will not only ensure service excellence but also inspire innovation in product development.
In conclusion, welding metal tubing is a dynamic process that demands a blend of expertise, precision, and technological prowess. Navigating the intricacies of different welding methods and maintaining rigorous standards of quality control are the hallmarks of excellence. By aligning practical experience with technical know-how, manufacturers can create superior tubing products that stand the test of time, setting benchmarks across industries for reliability and innovation.