welding hydraulic pipe
2 月 . 15, 2025 04:39

Welding hydraulic pipes involves a unique combination of technical expertise and practical experience to ensure optimal performance and reliability in hydraulic systems. As a vital component of various industrial applications, these pipes are crucial for transmitting hydraulic fluid under pressure, translating to precise mechanics and rigorous standards in their construction and maintenance.
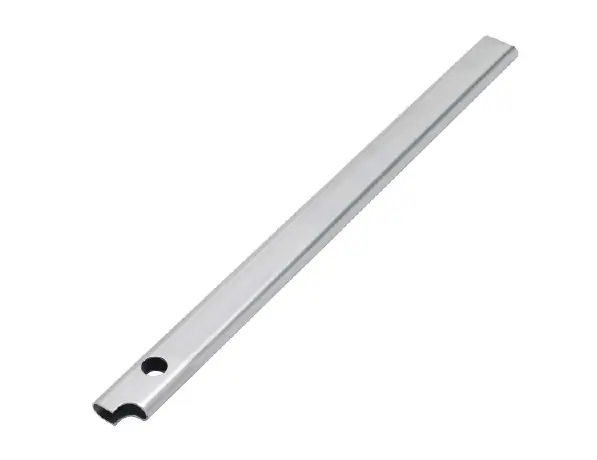
Hydraulic systems are intricate networks that transform fluid pressure into mechanical energy, powering machinery across industries ranging from construction and aviation to manufacturing. At the core of these systems lie hydraulic pipes, responsible for channeling hydraulic fluid efficiently. These pipes must withstand high pressures and harsh environments, making the welding process a critical factor in their integrity and performance.
Effective welding of hydraulic pipes mandates a blend of skills and industry knowledge. First and foremost, understanding the material composition of the pipes is crucial. Typically made from steel or stainless steel, these materials require specific welding techniques. The choice of welding method, such as TIG (Tungsten Inert Gas) or MIG (Metal Inert Gas), heavily depends on the material type, thickness, and operating environment of the hydraulic system.
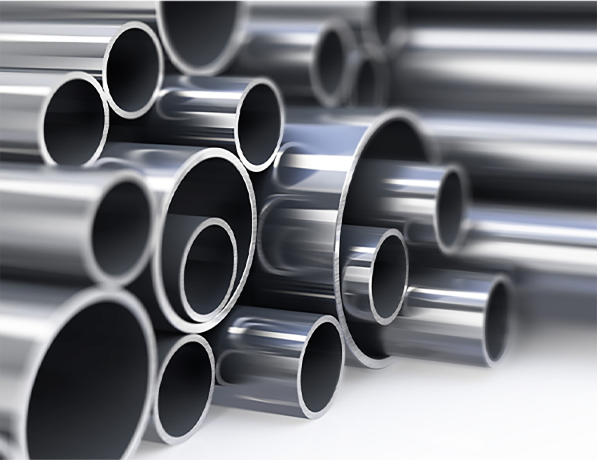
Expertise in welding hydraulic pipes begins with meticulous preparation. This involves cleaning the pipe surfaces thoroughly to remove any contaminants that could affect the quality of the weld. Rust, paint, oil, and other residues must be eliminated to prevent flaws that could compromise the pipe's integrity. Professionals utilize solvents or chemical cleaners specifically designed to prepare metal surfaces for welding.
Precision alignment of the pipes before welding is also imperative. Misalignment leads to stress points and potential leaks, jeopardizing system efficiency. Experienced welders use jigs and fixtures to ensure perfect alignment, employing precise measuring tools, such as calipers and squaring devices, to achieve exact dimensions.
During the welding process, maintaining proper heat levels and travel speed are crucial to prevent defects such as cracking, incomplete penetration, or excess distortion. Professionals are adept at adjusting these parameters in real-time, drawing on their deep understanding of welding dynamics and pipe behavior under thermal stress.
welding hydraulic pipe
Post-welding inspection and testing forms the final stage of guaranteeing the reliability of welded hydraulic pipes. Techniques like ultrasonic testing, radiographic examination, and pressure testing are employed to detect any weld defects invisible to the naked eye. These rigorous testing methods underscore the commitment to ensuring that each weld meets exacting standards and performs reliably in high-pressure environments.
Expert welders are also mindful of the challenges posed by the operating environments of hydraulic pipes. For instance, systems exposed to corrosive substances or extreme temperatures require special considerations in the selection of filler materials and protective coatings. Consulting industry standards, such as those issued by the American Society of Mechanical Engineers (ASME) or the International Organization for Standardization (ISO), ensures compliance and enhances the credibility of the welding work.
Furthermore, staying updated with technological advancements and emerging techniques in welding is essential for maintaining expertise. Automated welding processes and enhanced inspection technologies are reshaping the landscape, offering improved precision and efficiency. Professionals with a forward-thinking approach, who embrace these innovations, provide enhanced solutions that align with modern demands for speed, accuracy, and cost-effectiveness.
Trustworthiness in welding hydraulic pipes stems from a commitment to safety and reliability. Acknowledging the potential risks inherent in hydraulic systems, well-trained professionals adhere strictly to safety guidelines and employ personal protective equipment (PPE) such as welding helmets, gloves, and flame-resistant clothing. By conducting risk assessments and implementing robust safety measures, these experts ensure a safe working environment while delivering high-quality welds.
In conclusion, welding hydraulic pipes is a specialized field that demands a high level of expertise, experience, and trustworthiness. Through meticulous preparation, precise execution, and rigorous testing, industry professionals build authority and reliability in their work. By continually seeking knowledge and embracing innovations, they uphold the standards required for the seamless operation of hydraulic systems across diverse applications. As the backbone of numerous machines and structures, the integrity of hydraulic pipes is paramount, and those who master the art and science of welding them hold a vital role in ensuring their durability and performance.