welding header tubes
2 月 . 15, 2025 04:16

Welding header tubes is a critical process in various industrial applications, ranging from automotive manufacturing to power plants. The efficient and durable welding of these tubes can significantly impact the performance and longevity of the entire system. Professionals in the field understand that expertise and precision are paramount when approaching this task. This article explores the nuances of welding header tubes, providing valuable insights into best practices, tools, and techniques that ensure optimal results.
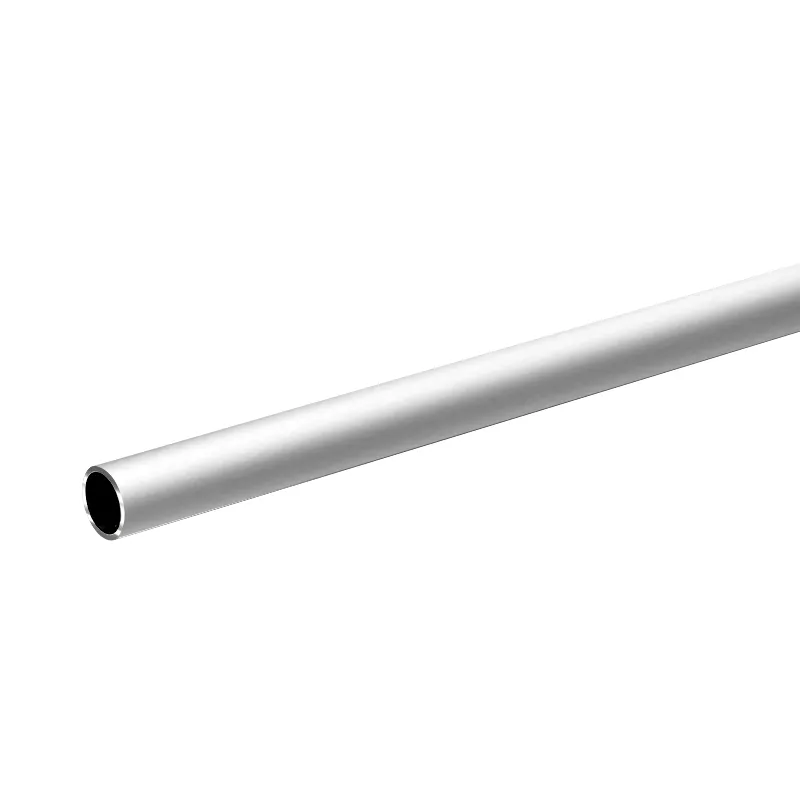
Header tubes often serve as vital components within larger piping systems, responsible for directing and distributing fluid, gas, or steam. Given their crucial role, the integrity of welds is of utmost importance. An experienced welder appreciates the necessity of selecting appropriate materials and welding processes tailored to the specific requirements of each project. For instance, the material composition of the tubes—whether stainless steel, carbon steel, or alloy—will dictate the selection of the welding method, such as TIG (Tungsten Inert Gas) welding or MIG (Metal Inert Gas) welding.
A deep understanding of welding metallurgy is essential when working with header tubes. The heat-affected zone (HAZ), the area of the base metal whose mechanical properties or microstructure have been altered by the welding heat, can become a point of vulnerability if not handled correctly. Skilled welders employ precise heat input control to minimize the negative effects on the HAZ, ensuring that the tube maintains its strength and corrosion resistance. Employing preheat and post-weld heat treatments further mitigates the risks of cracking and metallurgical inconsistencies.

High-quality welds on header tubes also rely on superior joint preparation and fit-up. Ensuring that the ends to be welded align correctly involves meticulous cleaning and bevelling of the tube edges. Eliminating contaminants, such as oil, grease, and rust, prevents weld defects and promotes sound fusion. The fit-up process, which aligns and secures the tubes before welding, must be executed with accuracy to avoid misalignment that could compromise the system’s efficiency and capacity.
In terms of equipment, investing in state-of-the-art welding machines and accessories significantly enhances the quality of tube welds. Modern welding equipment often incorporates advanced features like adjustable amperage control and pulse welding capabilities, which allow for precise heat management and reduced distortion. Using quality filler materials and shielding gases appropriate to the base metals further fortifies the weld area, ensuring a seamless and robust join.
welding header tubes
Safety cannot be overstated in the welding of header tubes. Professionals religiously adhere to safety standards and practices, such as wearing personal protective equipment (PPE) including helmets with appropriate filters, gloves, and flame-resistant clothing. Welding fumes, which can be hazardous, are effectively managed through proper ventilation systems, thus protecting workers and maintaining a safe working environment.
Quality assurance remains a cornerstone of successful header tube welding projects. Non-destructive testing (NDT) methods, such as ultrasonic and radiographic testing, are vital in verifying the integrity of welds. These tests help detect potential defects like voids, cracks, and inclusions that are invisible to the naked eye. Conducting thorough inspections before, during, and after the welding process upholds the overall quality and longevity of the system.
A trusted and authoritative figure in the welding community will constantly update their knowledge and skills. Continuous education in the latest welding technologies and techniques is necessary to remain competitive and deliver superior outcomes. Engaging with professional organizations and participating in workshops and seminars fosters a culture of learning and excellence.
In conclusion, the welding of header tubes demands a careful blend of expertise, precision, and commitment to quality. As we delve deeper into this specialized field, the nuances of materials, techniques, and safety measures reveal a complex but rewarding discipline that forms the backbone of many industrial applications. For those seeking excellence, attention to detail and a commitment to ongoing learning ensure that this craft will continue to thrive and evolve.