welded and drawn tubing
2 月 . 15, 2025 00:20

Welded and drawn tubing stands as a testament to engineering precision and metallurgical evolution, serving crucial roles across various industries due to its exceptional strength and adaptability. Designed to meet the high demands of today's technologically advanced sectors, this type of tubing excels in performance where precision and reliability are non-negotiable.

The manufacturing of welded and drawn tubing begins with a strip of metal that is first formed into a tubular shape and then welded along its seam. However,
it's the subsequent drawing process that truly enhances the physical properties of the tubing. By cold drawing the welded tubes through a series of dies, the material undergoes work hardening, significantly increasing its mechanical properties. This operation not only ensures uniform dimensional accuracy but also gives the tubes a finer microstructure, enhancing their strength and corrosion resistance.
From aerospace to automotive, welded and drawn tubing provides indispensable solutions. In the aerospace industry, its high strength-to-weight ratio makes it ideal for constructing components that must endure extreme conditions without adding unnecessary weight. Similarly, within automotive applications, such tubing contributes to the development of efficient, yet durable, brake lines and fuel systems, striking a balance between performance and safety.
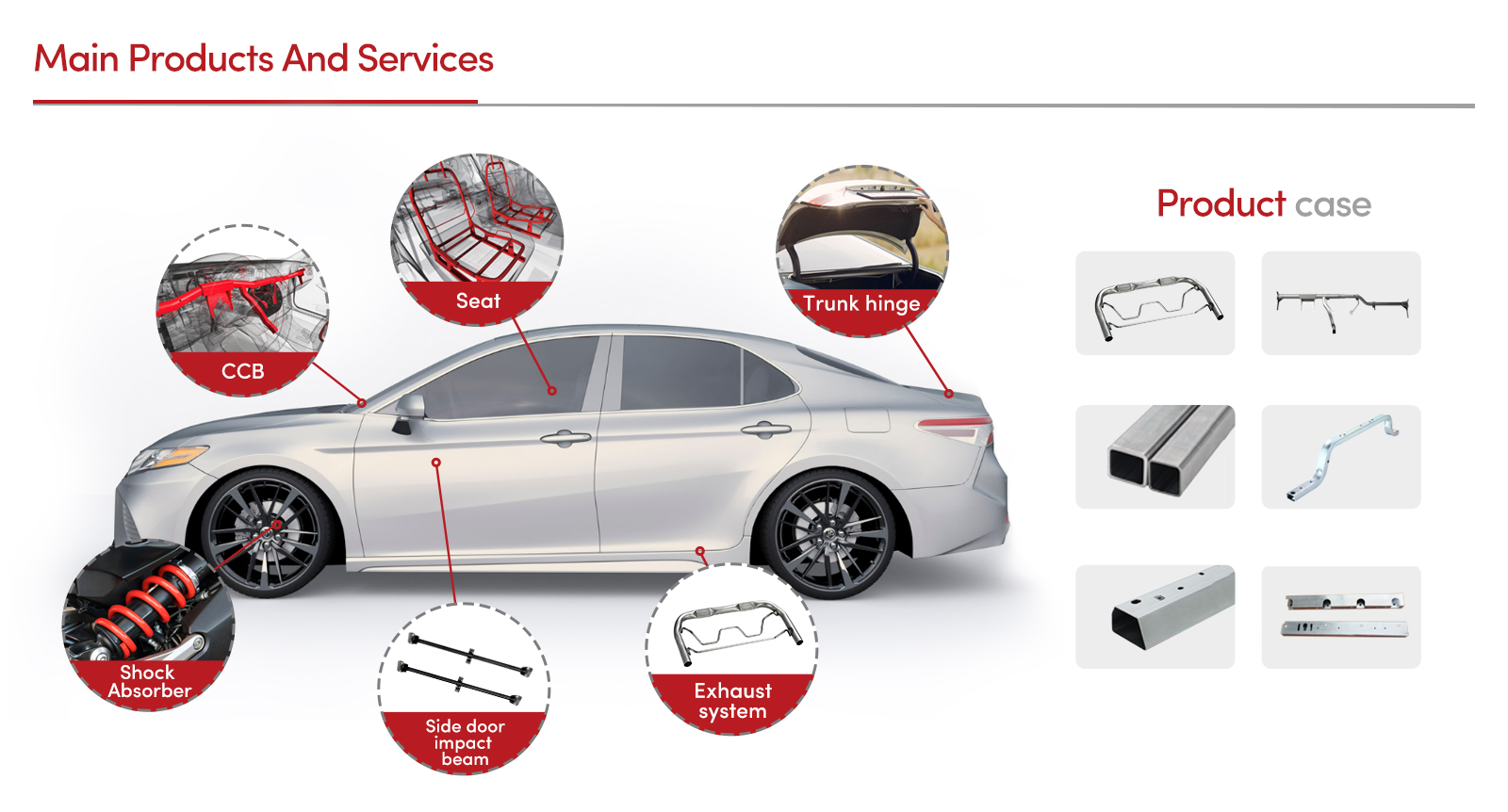
The healthcare sector also reaps benefits from the precision of welded and drawn tubing. Medical devices often demand high precision and reliability, with stainless steel tubing forming the backbone of many surgical instruments and hospital equipment. Its resistance to corrosion and bio-inert characteristics make it an invaluable resource in high-stakes environments where patient safety cannot be compromised.
Beyond practical applications, the quality control involved in producing welded and drawn tubing speaks volumes about its reliability and trustworthiness as a product. Each tube is meticulously tested for integrity and performance, conforming to stringent international standards. Whether it’s ultrasonic testing to detect weld seam flaws or dimensional assessments to ensure exact specifications, every step reflects a commitment to quality that stakeholders across industries have come to trust.
welded and drawn tubing
Moreover, the versatility of welded and drawn tubing extends to customizability, offering solutions tailored to specific needs. Manufacturers can adjust factors such as length, diameter, and wall thickness to accommodate the unique requirements of different projects, thereby promoting innovation and enhancing project outcomes.
Sustainability also finds its place in discussions around welded and drawn tubing. As industries move towards more sustainable practices, this type of tubing offers prolonged lifecycle benefits due to its durability and resistance to wear and tear. Recycling metal tubes also fits into broader environmental goals, making them a greener choice compared to alternative materials that may not boast the same recyclability or longevity.
Advances in technology and production techniques continue to push the boundaries of what is possible with welded and drawn tubing. High-definition inspection devices and automated production systems ensure that this product not only meets the current standards of quality and precision but continually exceeds them, setting new benchmarks in its domain.
Thus, welded and drawn tubing represents a fusion of expertise and innovation, cementing its role as a critical component in diverse applications. Its continued evolution stands as a testament to the industry's push towards enhancing performance while upholding safety and environmental standards, proving once again that in the world of industrial components, it is indeed a cornerstone material.