weldable tubing
2 月 . 14, 2025 23:42

Weldable tubing has become an essential component in various industries, from automotive to aerospace, due to its versatile application and robust characteristics. The success of projects often hinges on the quality and performance of this material. Therefore, understanding the full scope of weldable tubing, including its benefits, applications, and selection criteria, is critical for engineers and procurement specialists who seek optimal results.
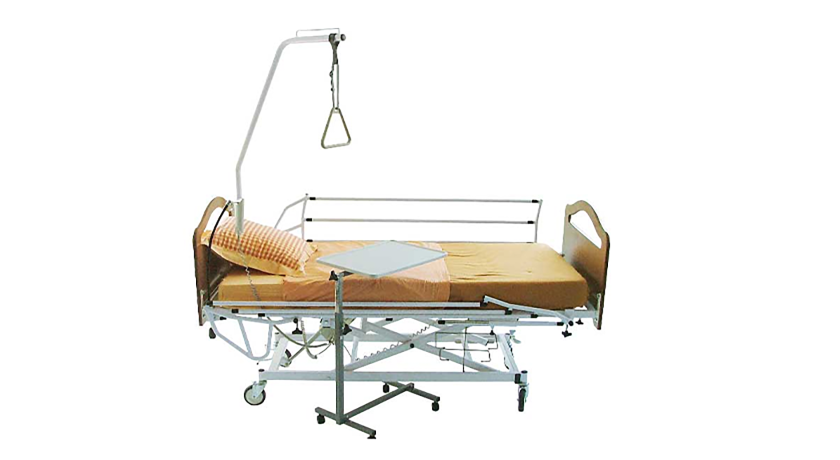
Weldable tubing refers to steel or alloy tubes specifically designed for welding applications. Its construction allows for easy manipulation and joining through various welding techniques such as TIG, MIG, and even laser welding. This adaptability makes weldable tubing an invaluable resource in design and manufacturing.
One of the primary advantages of weldable tubing is its strength-to-weight ratio. This property is particularly beneficial in the aerospace and automotive industries, where reducing weight without compromising structural integrity is crucial. In automotive engineering, the use of weldable tubing contributes to developing lighter and more fuel-efficient vehicles, aligning with the industry's shift toward sustainability. On the other hand, in aerospace, where materials must withstand extreme conditions, the resilience of weldable tubing ensures safety and reliability.
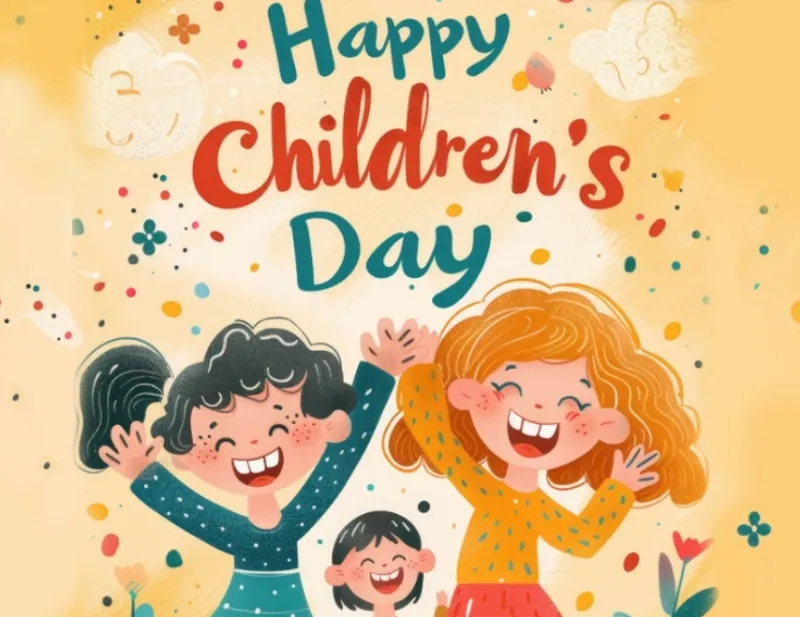
Additionally, weldable tubing provides significant customization possibilities. It comes in a range of materials, including stainless steel, carbon steel, and various alloys, each offering unique properties. For instance, stainless steel tubing is renowned for its corrosion resistance and aesthetic appeal, making it suitable for architectural applications, while carbon steel provides enhanced durability for industrial purposes. These material choices allow developers to select the most appropriate option for their specific needs, enhancing product longevity and performance.
The flexibility of weldable tubing extends further into its dimensional variance. Tubing can be customized in terms of diameter, wall thickness, and length to fit specific design requirements. This adaptability minimizes waste, reduces project costs, and streamlines the production process, which is vital in large-scale manufacturing scenarios.
weldable tubing
When selecting weldable tubing, several critical factors must be considered to ensure its effectiveness in application. First, understanding the environmental conditions is paramount. For projects exposed to harsh weather or chemical environments, corrosion-resistant materials like stainless steel may be preferred.
Another factor is the load conditions the tubing will endure. Accurate stress analysis and load capacity estimates must influence the choice of material and construction method.
Moreover, the choice of welding technique can affect the integrity of the final product. Professionals often rely on TIG or MIG welding for weldable tubing due to their precision and strength. TIG welding, with its high-purity welds, is particularly favored in applications where aesthetics and minimal contamination are priorities, such as in medical equipment manufacturing. In contrast, MIG welding offers speed and efficiency, suitable for high-volume production environments.
Incorporating weldable tubing in designs requires an expert understanding of metallurgical properties and welding technologies. Industry leaders often conduct extensive research and testing to optimize their use of weldable tubing, ensuring compatibility and compliance with safety standards. When done correctly, it enhances prosperity and innovation, allowing businesses to lead in quality and performance.
In conclusion, weldable tubing stands as a testament to engineering excellence and adaptability. The continued advancements in material science and welding technology only broaden its applications, solidifying its importance across multiple sectors. By carefully selecting the right kind of weldable tubing and appropriate welding techniques, businesses can achieve significant improvements in efficiency, durability, and cost-effectiveness, ultimately leading to a competitive edge in their respective fields. The choice of weldable tubing is not merely a logistical decision but a strategic one that influences the success of current and future undertakings.