tube welded
2 月 . 14, 2025 22:12

Tube welding has emerged as an essential technique in various industries, from automotive to aerospace, due to its ability to provide robust and durable joints. Understanding the intricacies of tube welding can lead to better product integrity and longevity, ensuring that the manufactured items can withstand the rigors of their intended use.

The process of tube welding is not as straightforward as it might seem at first glance. Various methods, such as Tungsten Inert Gas (TIG) welding, Metal Inert Gas (MIG) welding, and Laser Welding, each offer distinct advantages depending on the application. Expertise in selecting the appropriate method is imperative for achieving optimal results. For instance, TIG welding is lauded for its precision, making it ideal for applications where a clean, high-quality finish is necessary. On the other hand, MIG welding might be preferred for projects where a faster process is needed without compromising strength.
When approaching tube welding, the material composition significantly impacts the welding technique employed. Materials such as stainless steel, aluminum, and carbon steel each present unique challenges and require different handling approaches. The expertise of the welder comes into play, where understanding the properties of different metals can drastically affect the quality of the weld. For example, aluminum's lower melting point necessitates a careful control of heat input to prevent distortion, while stainless steel requires adequate post-weld treatments to avoid corrosion.
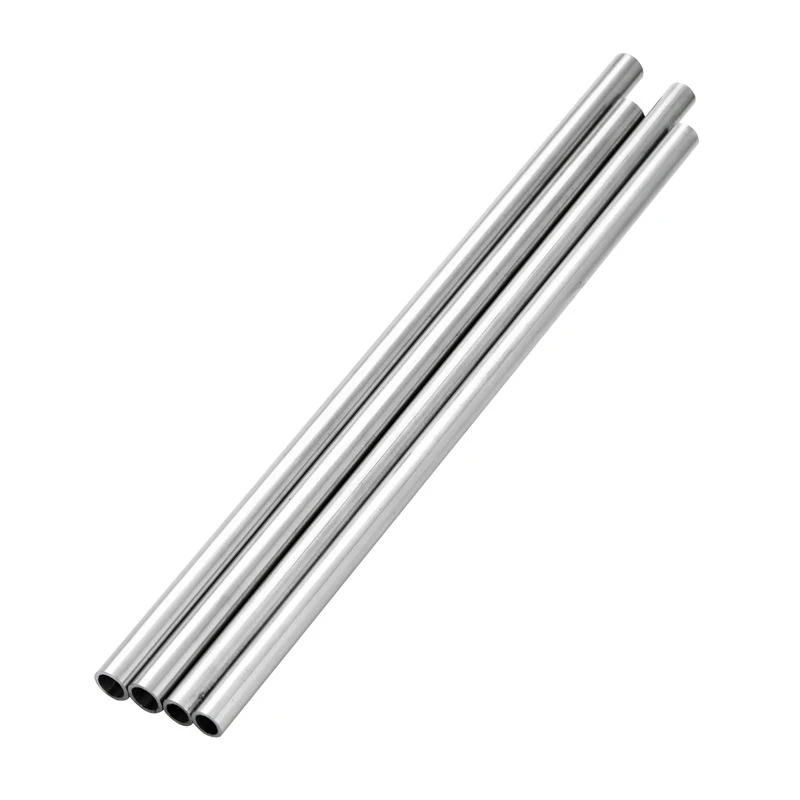
Experience in tube welding often translates into a keen eye for details that might otherwise be overlooked. An experienced professional intuitively knows to account for aspects like weld penetration and bead formation, directly influencing the weld's strength and finish. Mastering the balance between heat input and travel speed is crucial to avoid defects such as porosity or incomplete fusion. These seemingly minor details can be the difference between a successful weld and a failed product, highlighting the importance of knowledgeable welders.
tube welded
Authoritativeness in the field of tube welding is often demonstrated by adherence to industry standards and certifications. Compliance with standards such as those set by the American Welding Society (AWS) not only ensures safety but enhances the credibility of the welding process. Companies that insist on certified welders showcase their commitment to quality, reassuring clients of their dedication to excellence.
Trustworthiness, a pivotal pillar in the world of tube welding, begins with the transparency of the welding process. Reputable professionals provide comprehensive insights into their procedures, guaranteeing that every weld adheres to the highest industry standards. This transparency fosters trust as it assures clients that there are no shortcuts taken, and the structural integrity of the weld is as robust as promised.
In addition to this, the adoption of advanced technology can fortify trust in tube welding practices. The utilization of automated systems ensures not only enhanced precision but also consistency in weld quality across high-volume production. Technologies such as real-time weld monitoring systems enable welders to detect and rectify potential issues instantaneously, thereby reducing the risk of defects and ensuring consistent product quality.
To conclude, tube welding is a complex process that demands a blend of experience, expertise, authoritativeness, and trustworthiness. Mastery of these elements ensures the provision of high-quality products that serve their purpose with reliability and durability. For businesses and clients alike, understanding the nuances of tube welding will invariably lead to better decision-making, higher-quality products, and ultimately, greater satisfaction in the end-use applications. Thus, as industries continue to evolve, so too must the practices and technologies associated with tube welding, pushing the boundaries of what is possible with this critical industrial technique.