Car Back Support Steel Tube
2 月 . 14, 2025 21:42

Tube sheet welding is an intricate process that plays a crucial role in the fabrication of heat exchangers and pressure vessels. This sophisticated technique requires not only proficiency and precision but also deep knowledge of materials science and welding technology. Achieving a durable and leak-proof joint is paramount, as it influences the integrity and performance of the entire assembly. This article delves into the professional insights and authoritative findings surrounding tube sheet welding to provide a reliable source for industry professionals.
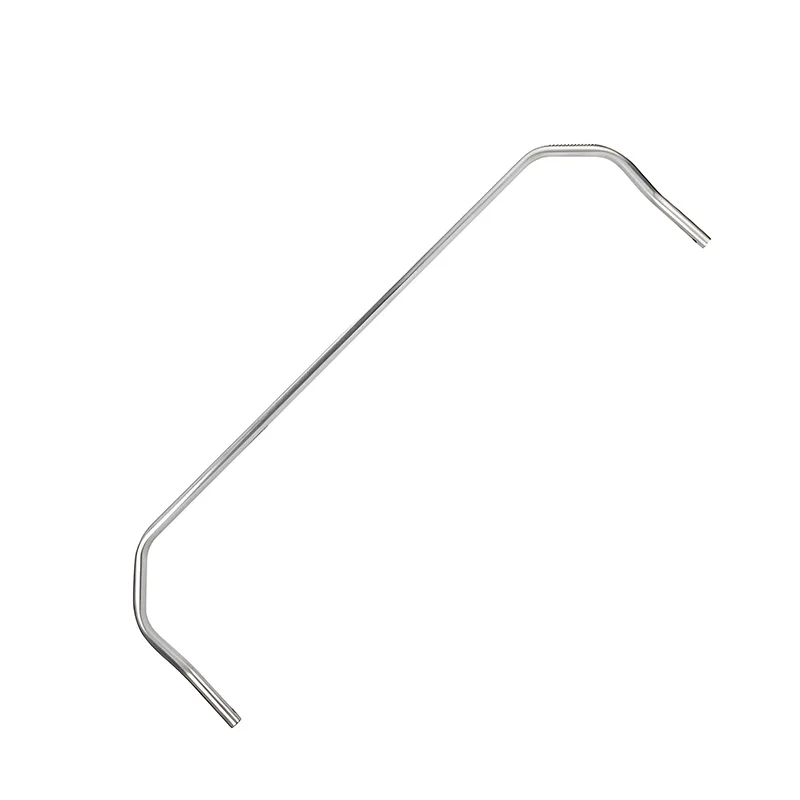
In the realm of heat exchanger fabrication, the tube sheet serves as a pivotal component. Its primary function is to support and hold the tubes in position, ensuring fluid containment and optimal heat transfer. The welding of tube sheets, therefore, must be executed with meticulous attention to detail and adherence to stringent standards to prevent potential failures that could result in catastrophic operational consequences.
From the perspective of expertise, the welding of tube sheets typically involves a variety of techniques, including TIG (Tungsten Inert Gas) welding, MIG (Metal Inert Gas) welding, and submerged arc welding. The choice between these methods depends on several factors such as the material of the tube and sheet, the thickness of the components, and the operational environment of the heat exchanger or pressure vessel.
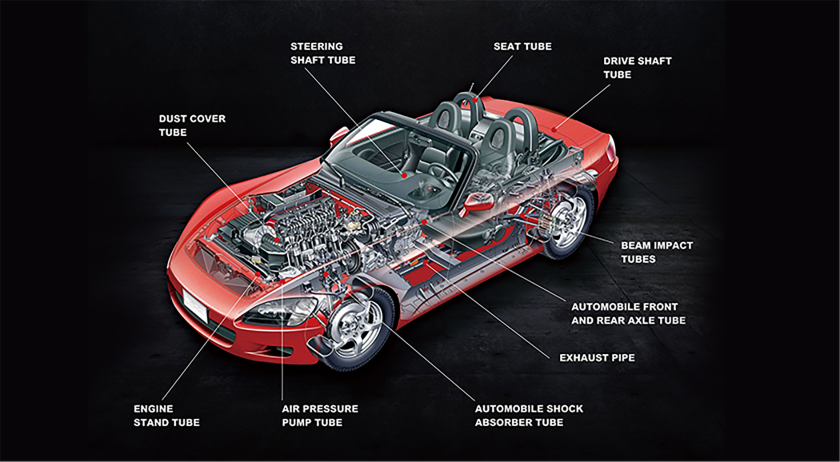
TIG welding, renowned for its precision and control, is often preferred for thin materials and applications where high-quality welds are essential. It provides excellent control over the heat input, which is critical for preventing warping and distortion of the tube sheet. MIG welding, on the other hand, offers speed and efficiency, making it suitable for thicker materials and when productivity is a priority. Submerged arc welding, while not as common for tube sheets due to its limitation with smaller components, can be used effectively in specific scenarios where deep penetration and minimal spatter are required.
Materials selection also stands as a cornerstone of tube sheet welding. Common materials include carbon steel, stainless steel, and various nickel alloys.
Each of these materials presents unique challenges and requires a tailored approach to welding. For instance, stainless steel is susceptible to distortion and requires careful heat management during the welding process. Nickel alloys, often used in high-temperature applications, demand a sophisticated understanding of metallurgy to ensure practicable weldability without compromising material properties.
tube sheet welding
Authoritative resources emphasize the importance of pre-weld and post-weld preparations. Proper edge preparation, cleaning, and alignment are critical steps in pre-welding, all aimed at ensuring optimal fusion and minimizing defects. Post-weld heat treatment may be necessary to relieve internal stresses, enhance corrosion resistance, and stabilize the microstructure of the weld joint.
Experience in tube sheet welding underscores the significance of inspection and testing. Non-destructive testing (NDT) methods, such as radiographic testing and ultrasonic testing, are invaluable in detecting potential weld defects without compromising the weld. Hydrostatic testing is another widely used practice for assessing the integrity and leakage resistance of the tube sheet assembly.
The credibility of tube sheet welding processes is rooted in well-documented standards and specifications. Adherence to codes such as ASME (American Society of Mechanical Engineers) Boiler and Pressure Vessel Code and API (American Petroleum Institute) standards ensures that welds meet essential safety and quality criteria. These codes provide comprehensive guidelines on materials, design, fabrication, inspection, testing, and certification, thereby cementing the trustworthiness of tube sheet welding applications.
Product innovation and technological advancements continue to reshape the landscape of tube sheet welding. Automated welding systems, while requiring significant capital investment, offer enhanced consistency and precision, reducing the probability of human error. Additionally, real-time monitoring and control systems are being integrated to track welding parameters, ensuring compliance with desired specifications throughout the process.
In conclusion, tube sheet welding is a domain where expertise and authoritative knowledge converge to produce reliable and high-performance industrial components. By prioritizing the principles of material selection, exact welding techniques, rigorous testing, and conformance to established standards, professionals can deliver tube sheet welds that not only fulfill but surpass industry expectations. The continuous evolution of welding technologies and methodologies further bolsters the quest for excellence in tube sheet welding, offering promising vistas for future advancements in the field.