tube bending and welding
2 月 . 14, 2025 10:39

In the world of modern manufacturing, the processes of tube bending and welding have taken center stage due to their significant role in creating complex structures and intricate designs. Companies across various industries, from automotive to aerospace, rely on advanced tube bending and welding techniques to deliver high-quality products that meet stringent standards. As technology advances, so does the expertise required to expertly bend and weld tubes, making it a specialized field that calls for both precision and knowledge.

Tube bending, a process that might appear straightforward at first glance, requires a deep understanding of materials and methods. Steel, stainless steel, aluminum, copper, and titanium each have unique properties that influence how they can be bent without compromising structural integrity. For instance, bending a stainless steel tube demands meticulous attention to its springback effect—a phenomenon where the tube tries to revert to its original shape after bending. This is where experience becomes invaluable. Veteran technicians leverage their profound understanding of materials to predict these nuances and adjust their techniques accordingly, ensuring the final product meets desired specifications.
Modern tube bending is also heavily reliant on CNC (Computer Numerical Control) technology. This technological leap permits unparalleled precision and repeatability, crucial elements for industries where even the slightest deviation can lead to costly failures. Experienced operators understand the importance of precise calibration and programming in CNC machines to achieve complex bends without deformation or wrinkling of the tube. The expertise involved in operating these machines is not merely dependent on technical knowledge but also practical experience gained through years of hands-on practice in the field.
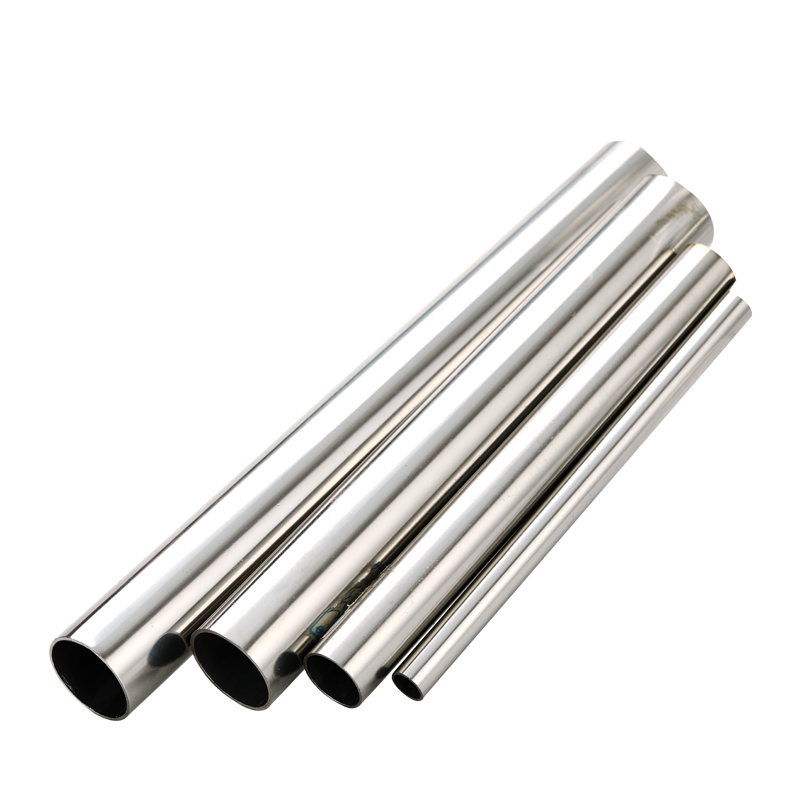
However, bending is only part of the equation. Welding, the process of joining two or more pieces of metal together, is equally critical in ensuring the structural integrity and functionality of the final product. Welding in the context of tube fabrication must account for factors such as joint design, material thickness, and weld seam positioning. Expert welders possess a profound mastery over different welding techniques, including MIG (Metal Inert Gas), TIG (Tungsten Inert Gas), and laser welding, each offering distinct advantages and limitations.
TIG welding, for example, is preferred for its precision and control, making it ideal for thin-walled tubes where heat distortion needs to be minimized. Meanwhile, MIG welding might be selected for its speed and efficiency in welding thicker materials. The choice of welding technique plays a pivotal role in the durability and performance of the final product, which is why authoritative welders make these decisions based on a thorough understanding of metallurgy and engineering principles.
tube bending and welding
Trustworthiness in tube bending and welding comes from consistent quality outputs and meeting regulatory standards. Companies that have established themselves as leaders in this field invest heavily in quality control processes, including rigorous testing and inspection protocols like X-ray inspection, hydrostatic testing, and destructive testing methods. These measures ensure that every bent and welded tube not only meets client expectations but also adheres to safety and regulatory requirements.
Moreover, authoritative tube bending and welding firms frequently engage in collaborative innovation with clients, tailoring solutions that address specific challenges and requirements. This collaboration often results in custom tooling designs that push the boundaries of what is achievable, further solidifying their expertise and trustworthiness in the industry.
The landscape of tube bending and welding is continuously evolving, with advancements in material science and automation technologies leading the charge. Being part of this dynamic field requires a commitment to ongoing education and skill enhancement. Leading professionals understand the necessity of staying informed about the latest trends, techniques, and technologies. Participating in industry workshops, certifications, and seminars are crucial for maintaining both personal expertise and the company's authoritative standing.
In summary, mastering the art of tube bending and welding extends beyond technical ability, encompassing a profound understanding of materials, technology, and innovative practices. Companies that showcase genuine experience, expertise, authoritativeness, and trustworthiness in their processes remain at the forefront of this specialized field, delivering exceptional quality products that drive success across industries. The value they provide is measured not just in the precision of their work, but in the lasting partnerships they forge with clients who depend on their specialized skills and knowledge.