Trunk Hinges
2 月 . 14, 2025 21:13

Sterile tube welding is an essential process in industries requiring high standards of hygiene, such as pharmaceuticals, biotechnology, food processing, and semiconductor manufacturing. Ensuring the sterility of welds is crucial to maintaining product integrity and safety, preventing contamination, and adhering to regulatory compliance.
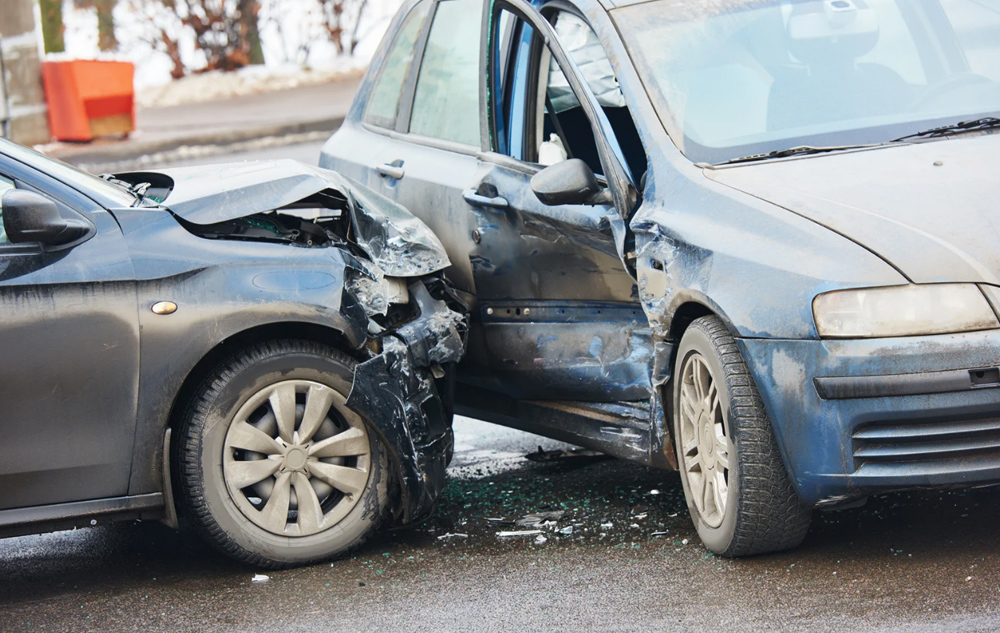
True tales from the manufacturing frontline reveal that the quest for sterility in tube welding is both art and science. Success demands understanding both the processes involved and the sophisticated equipment used. As a seasoned welding engineer, I've delved deep into these operations, witnessing firsthand the transformative power of innovative sterile welding techniques.
Firstly, the sterile tube welding process breaks down into specific steps, each pivotal to achieving perfect welds.
The procedure begins with thorough preparation. Tubing materials, typically stainless steel or specialized alloy, are meticulously cleaned to remove any potential contaminants. Clean environments are indispensable; typically, this occurs in controlled cleanroom settings with precise environmental controls.
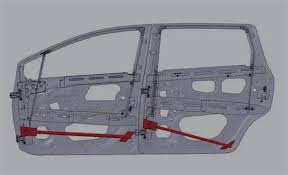
Cutting-edge welding technology here is exemplified by orbital welding. This automated process, characterized by its rotating welding arc around a stationary workpiece, guarantees uniform, robust, and contamination-free welds. It excels in joining thin-walled tubes, a common requirement in sectors like pharmaceuticals where tube diameter consistency is critical for maintaining integrity and preventing leaks.
High-end orbital welding machines now integrate programmable welding parameters, real-time monitoring, and diagnostics, enhancing precision while reducing human error. Technology's development continually refines these machines, providing operators with user-friendly interfaces to tailor weld settings precisely to their batch requirements. The result? Consistently sterile welds and minimal deviation from specifications.
sterile tube welding
Industry professionals bear testimony to the reliability of sterile tube welding in maintaining sterility and system integrity. Repeated assessments and pressure tests assure the robustness and reliability of the welds, crucial in sectors where failure can lead to dire repercussions. Regular training and certification for operators on the latest equipment and evolving welding standards ensure sustained expertise and capability in the workforce.
Verification of sterile welding is not merely procedural but existential, where adherence to globally recognized standards such as ASME BPE and ISO 14644 shapes reputations and market standing. Compliance builds trust, offering clients peace of mind that their products maintain the highest standards of safety and performance. Regular third-party audits and certifications act as additional layers of assurance in the maintenance of sterile environments.
Exploring the niche of sterile tube welding reveals a field where precision engineering meets dedicated craftsmanship. The authoritative insights of seasoned practitioners elevate this beyond mere function, into a realm of critical importance for modern industry. Their narratives and deep expertise offer a formative framework that businesses can utilize to elevate their operational standards.
Ultimately, the story of sterile tube welding's evolution is one of constant innovation, ceaseless adaptation, and commitment to excellence. For businesses seeking stainless steel tubing solutions that marry cleanliness with cutting-edge technology, this welding process stands as both a challenge and a promise—a challenge to meet ever-advancing standards, and a promise to safeguard the purity and safety of our essential industries.