stainless steel welded tube
2 月 . 14, 2025 08:31

In the dynamic realm of industrial materials, stainless steel welded tubes hold a pivotal position, celebrated for their versatility and strength. As industries evolve, the demand for materials that combine durability with cost-effectiveness grows. This evolution calls for a closer look into the stainless steel welded tube – a product that not only stands the test of time but is engineered to meet diverse industrial needs.

Stainless steel welded tubes are crafted through the intricate process of welding, unlike their seamless counterparts. This method involves rolling steel sheets or strips into a tube shape and then welding the seam. The precision in the welding process is paramount, as it ensures the integrity and strength of the tube. It’s this exacting process that distinguishes superior quality tubes from the rest. In industries where structural strength is non-negotiable, such as construction, automotive, and energy, the importance of reliable welded tubes cannot be overstated.
One of the most significant advantages of stainless steel welded tubes is their unparalleled resistance to corrosion. In environments exposed to moisture, chemicals, or extreme temperatures, they perform exceptionally well by maintaining their structural integrity and appearance. This characteristic makes them a cost-effective choice for long-term projects. Real-world applications underscore this advantage, as seen in plumbing systems where tubes are consistently exposed to water or in chemical plants where they come in contact with hazardous substances.
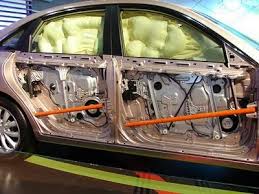
Professional insight reveals another critical facet the variety of stainless steel grades available for welded tubes, each tailored for specific applications. AISI 304 and 316, for example, are popular grades chosen for their balance of malleability, durability, and corrosion resistance. Experts emphasize the need to select the appropriate grade depending on the environmental conditions and mechanical demands of the application. This expertise ensures that the tubes do not falter during operation, thus maintaining project integrity.
In terms of fabrication and usage, stainless steel welded tubes offer impressive adaptability. Engineers appreciate their ease of installation, which translates to reduced labor costs and time savings. Moreover, these tubes can be custom-formed to meet specific project designs, including customised diameters and lengths, without compromising their performance. This versatility is particularly beneficial in architectural projects, where aesthetic considerations are as crucial as functionality.
stainless steel welded tube
Beyond their physical properties, the production and utilization of stainless steel welded tubes align with modern sustainability standards. The recycling capabilities of stainless steel contribute to reduced environmental impact, aligning with global efforts to promote green practices. This contributes to their growing popularity in projects that prioritize environmental conservation alongside economic feasibility.
Authoritative voices in the materials engineering domain advocate for the use of advanced welding technologies, such as laser welding, to enhance the quality and longevity of welded tubes. These technologies ensure a cleaner, more precise weld, which in turn reduces the risk of defects that could compromise the tube’s performance under duress. Professionals advise periodic quality checks and maintenance routines to monitor the condition of the welded tubes, ensuring any minor issues are addressed before they escalate.
Trustworthiness in the selection and sourcing of stainless steel welded tubes is paramount. Industry veterans recommend partnering with manufacturers who adhere to international quality standards and certifications. This not only guarantees the performance of the products but also fosters a level of assurance in clients regarding the safety and efficacy of their projects.
In conclusion, stainless steel welded tubes stand out as a cornerstone in modern industrial applications. Their robustness, combined with flexibility and sustainability, makes them an indispensable choice for engineers and architects alike. By embracing innovative welding techniques and committing to stringent quality controls, manufacturers continue to enhance the reliability and appeal of these tubes, securing their place as a preferred solution in the ever-evolving landscape of industrial materials.