seamless steel tube manufacturing process
2 月 . 12, 2025 19:38

The seamless steel tube manufacturing process is a fascinating journey that combines the rigor of engineering with the precision of modern technology to produce a product that is both versatile and indispensable in numerous industries. This process, while complex, is a testament to industrial excellence, providing a deep dive into the heart of modern manufacturing.
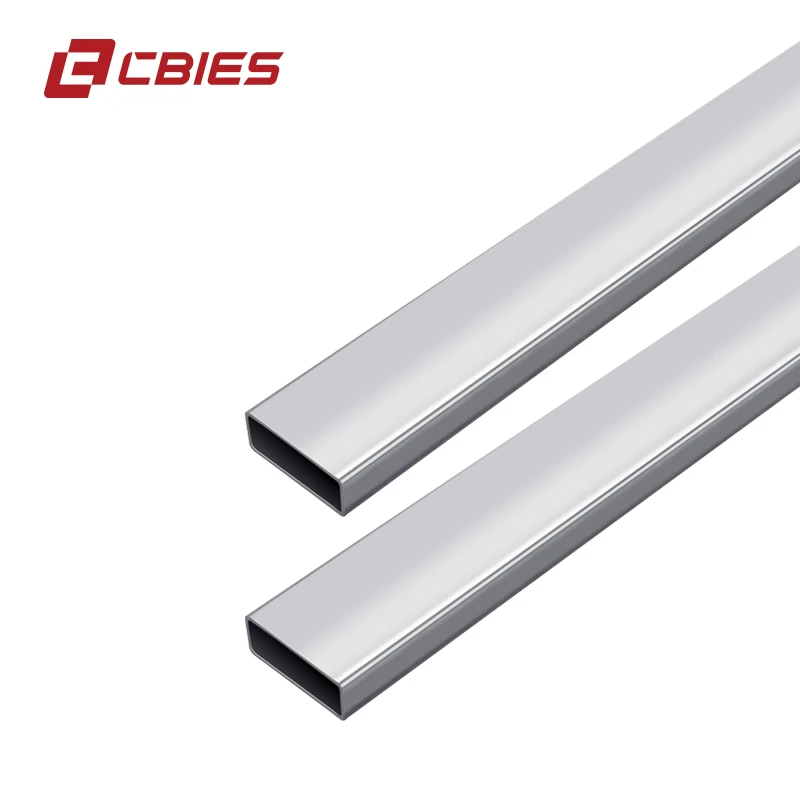
Seamless steel tubes are cylindrical conduits made from solid pieces of steel that are heated and then either pierced or drawn over a mandrel to form the desired tube shape. Unlike welded tubes, seamless tubes have no seam or weld joint, which significantly enhances their strength and durability—key factors in industries where safety and reliability are paramount.
The process begins with the selection of high-quality steel, usually in the form of billets or bars, chosen for their specific chemical composition and mechanical properties. These raw materials undergo rigorous quality checks to ensure that they meet industry standards and specific project requirements. This selection is the first step in a chain of quality assurance measures that emphasize the importance of using superior materials to achieve optimal product integrity.

Once the raw steel is selected, it is heated to temperatures exceeding 1200 degrees Celsius in a rotary furnace. This extreme heat treatment is crucial for softening the metal, making it malleable enough to be shaped into tubes. Experienced engineers and technicians precisely control this stage to maintain the integrity of the steel’s chemical composition—a skill honed through years of industry expertise.
After heating, the steel billet is transferred to a piercing mill where it undergoes a rotary piercing process. Here, the billet is pierced through its center by a pointed mandrel and an arrangement of rollers that help to elongate and shape the billet into a hollow tube. This step, known as cross-rolling, requires meticulous attention to detail and precision engineering to avoid any deviation that could compromise the tube’s internal surface quality.
The pierced billet, now resembling a thick-walled tube, continues to the elongation process. The tube is stretched, either through hot rolling or cold drawing, to achieve the desired diameter and wall thickness. This phase is critically dependent on the expertise of the operators and the technological capability of the machinery involved. Advanced monitoring systems and real-time adjustments ensure the tube maintains uniformity and consistent physical properties throughout its length.
seamless steel tube manufacturing process
Subsequent to elongation, the tube undergoes sizing and finishing processes where it is cut to length and subjected to a series of treatments to enhance its mechanical properties, surface finish, and dimensional accuracy. This may include heat treatments like annealing or quenching and tempering, which balance the hardness and ductility of the steel. The result is a seamless steel tube that meets precise specifications and can withstand severe operating environments.
Quality control in seamless steel tube manufacturing does not end with the production process. Each tube is rigorously inspected for defects using non-destructive testing methods such as ultrasonic testing and electromagnetic testing. These inspections are vital for ensuring the structural integrity of the tubes, which is crucial in applications such as oil and gas exploration, automotive, and structural engineering where failure can lead to catastrophic outcomes.
The seamless steel tube manufacturing process is a quintessential example of how industrial expertise, precision technology, and rigorous quality control come together to produce a high-performance product. It is a domain where professional knowledge and authoritative processes are critical to achieving the highest standards of trustworthiness and reliability.
The experience gained from years of iterations and innovations in seamless steel tube production has established the industry as a linchpin in manufacturing sectors across the globe. As demand for seamless steel tubes continues to grow, driven by their reliability and performance, the manufacturing process will inevitably evolve, incorporating cutting-edge technologies to further enhance production efficiency and product quality.
In conclusion, the seamless steel tube manufacturing process epitomizes the confluence of engineering expertise and industrial precision. It underscores the importance of using the right materials, employing skilled human resources, and adhering to stringent quality protocols to produce a product that is integral to the safety and success of countless applications worldwide.