Hydraulic Cylinder Seamless Steel Tube
2 月 . 14, 2025 17:46

Round tube welding is an intricate process requiring expertise, precision, and the right equipment to ensure a perfect seam every time. This task, often overlooked by many, is fundamental in industries ranging from automotive to construction, fulfilling both structural and aesthetic needs.
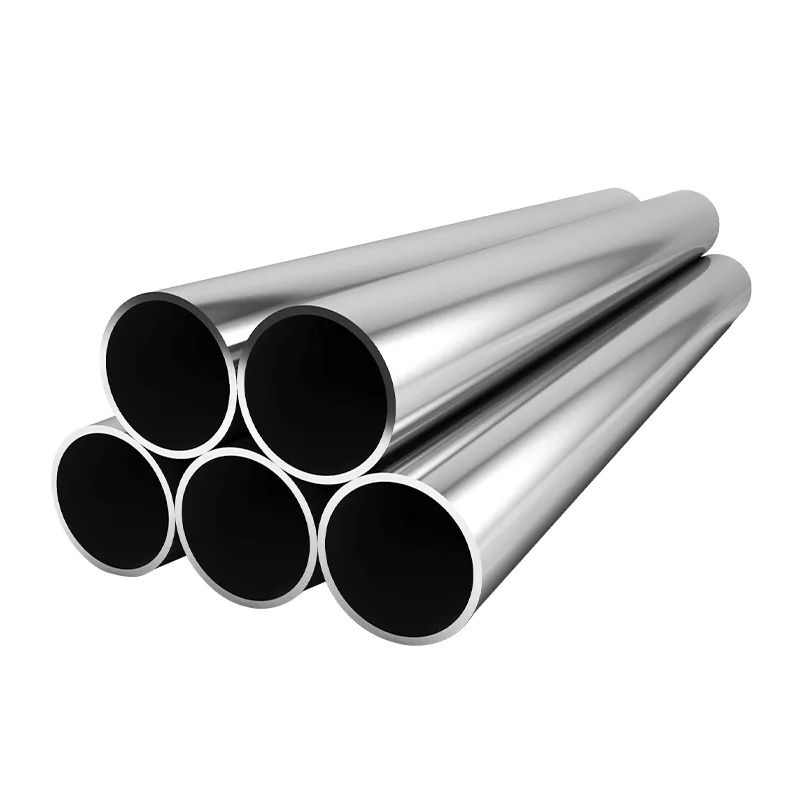
Imagine a bicycle frame or the supporting structure of a high-rise building – the durability and integrity of these essential items largely rely on the quality of round tube welding. As an experienced professional in this field, it's clear that not all welds are created equal and mastery over the process can significantly distinguish a satisfactory job from an exceptional one.
At the heart of successful round tube welding is the choice of technique. Whether it's MIG, TIG, or Oxy-Acetylene welding, each has its own set of benefits suited for specific applications. TIG welding, for instance, is renowned for its precision and clean finish, making it the preferred choice for projects where aesthetics are paramount. This method allows for greater control, facilitating intricate design work that boosts both product performance and visual appeal.
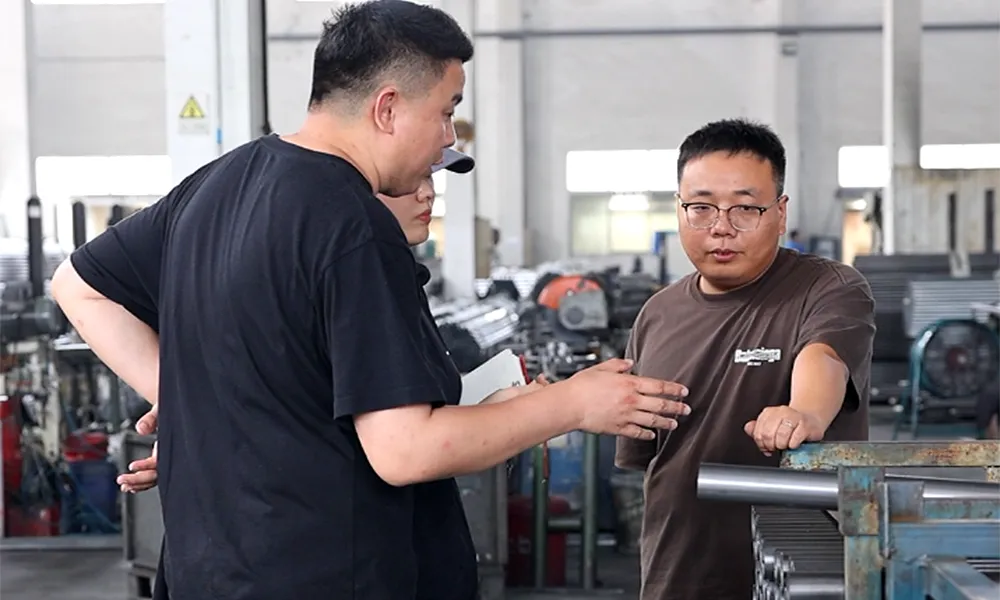
In discussing the technology of round tube welding, the emphasis should be placed on the equipment used. Investing in high-quality welding machines can markedly improve the outcome. Machines that offer adaptive controls can accommodate various alloys and enable welders to maintain consistency, which is crucial when working with different tube thicknesses and diameters. Additionally, the deployment of robotic welding arms in large-scale manufacturing has transformed the industry, increasing both speed and accuracy, thereby setting new standards for quality.
Worker expertise also plays a pivotal role in ensuring reliable welds. It's essential for welders to undergo rigorous training, preferably accompanied by certifications from recognized institutions. A certified welder not only possesses skills but also the knowledge to troubleshoot issues swiftly, reducing downtime and maintaining productivity. This expertise ensures welds that meet stringent industry standards and pass rigorous quality inspections.
round tube welding
Another critical factor often overlooked is the workspace environment. For optimal results, welders should operate in clean, well-ventilated areas that reduce contamination risks and provide a safe working space. The stability of the working conditions enhances the quality of the welds and supports better long-term outcomes, proving beneficial both economically and operationally.
Moreover,
understanding the science behind materials being welded is crucial. Different metals have unique properties and require different handling techniques. For instance, welding stainless steel tubes necessitates controlling heat input to prevent warping or compromising the metal’s structural integrity. Knowledge of metallurgy allows for the adaptation of techniques to cater to these requirements, ensuring a robust weld.
To build trust and demonstrate authority in round tube welding, showcasing a portfolio of successful projects can be invaluable. Demonstrating a track record of meeting specific industry needs and addressing complex welding challenges reinforces credibility. Collecting and presenting data, such as tensile strength measurements and durability tests from past projects, acts as compelling evidence of expertise.
Lastly, an ongoing dedication to learning about advancements and innovations in welding technology will maintain a competitive edge. The industry is ever-evolving, and staying informed about new techniques, equipment, and materials can drive business growth and client satisfaction. A commitment to continuous improvement secures a trusted position in the field.
In conclusion, mastering round tube welding encompasses not just technical skills but a deep understanding of materials, the right equipment, a controlled environment, and a commitment to ongoing education. This multifaceted expertise positions professionals as leaders in the industry, capable of delivering high-quality, reliable results that meet the exacting demands of clients seeking both function and form in their welded products.