Cloud gray mushroom style stacked stones
2 月 . 06, 2025 06:27

In the bustling world of automotive manufacturing, plastic injection molding has emerged as a groundbreaking process that empowers the industry with unparalleled efficiency and precision. As an expert in this field, having collaborated with numerous automotive giants over the years, I can attest to the transformative impact this technology has brought to vehicle components production. Its application not only enhances the production speed but also improves product durability, paving the way for a revolution in automotive parts manufacturing.
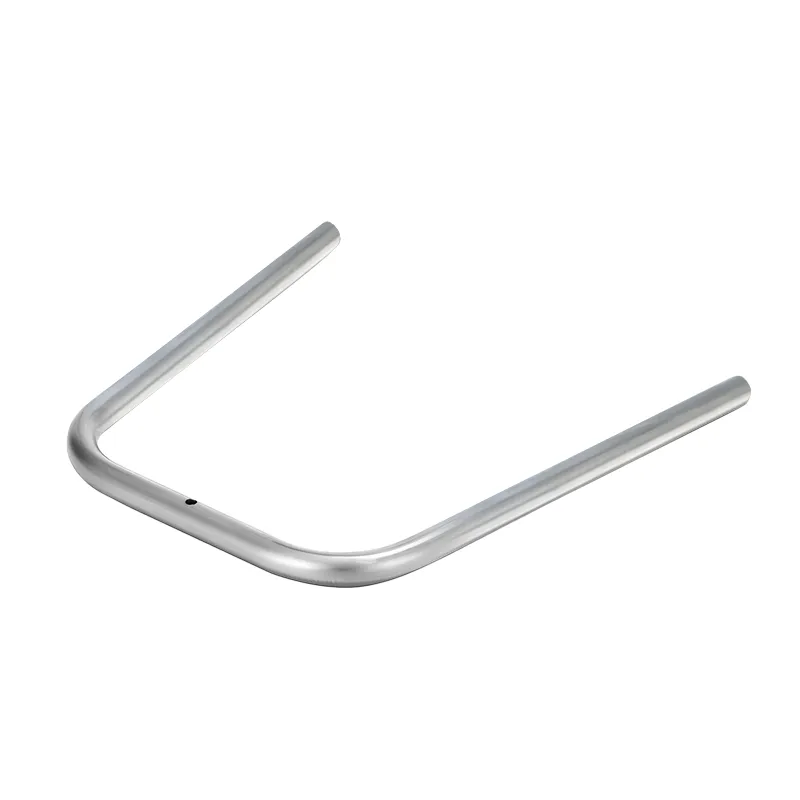
Plastic injection molding stands as a cornerstone in producing automotive components due to its unmatched ability to create complex and detailed parts efficiently. This process begins with feeding plastic pellets into a heated barrel, where they are melted and then injected into a mold cavity. The material then cools and hardens into the final product. This method allows manufacturers to produce intricate and lightweight parts which are essential in modern vehicle design, aiming for improved fuel efficiency and reduced emissions.
Experience has shown that the adaptability of plastic injection molding makes it ideal for automotive applications. With modern vehicles requiring components that cater to both performance and aesthetic purposes, the ability to swiftly switch from one design to another is invaluable. Plastic injection molding offers this flexibility, allowing for rapid prototyping and adjustments based on the dynamic demands of the automotive market. Manufacturers can thus keep pace with technological advancements and consumer preferences without incurring the prohibitive costs associated with traditional manufacturing methods.
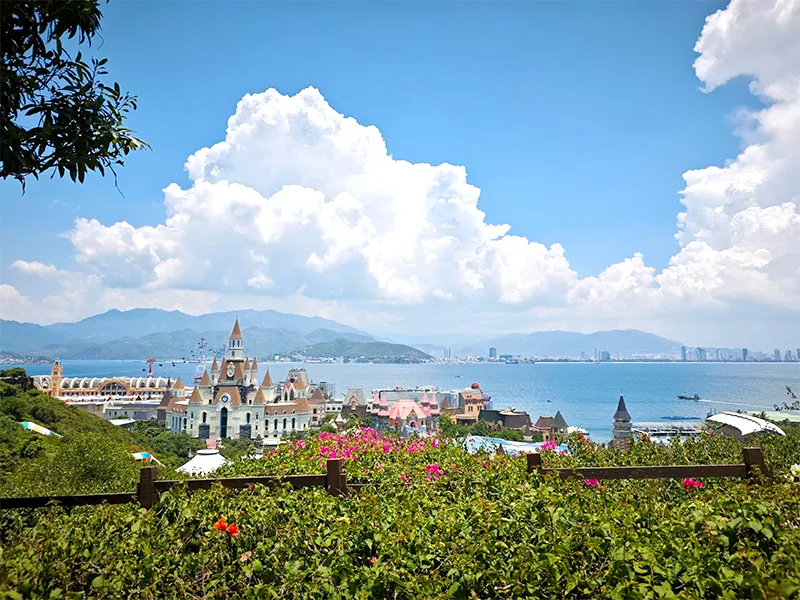
In the realm of expertise, it's not just about producing parts; it's about producing superior parts that meet rigorous industry standards. Advanced materials such as high-performance thermoplastics are employed in injection molding to provide enhanced strength, impact resistance, and thermal stability. These materials are crucial in the automotive sector, where components are often subjected to extreme conditions. From dashboards to engine blocks, critical components benefit from injection molding’s precision, reducing the risk of failure and enhancing the overall reliability of the vehicle.
plastic injection molding automotive parts
Authoritativeness in plastic injection molding is demonstrated through compliance with international standards and regulations that govern automotive manufacturing. Leading manufacturers have adopted ISO certifications and adhere to industry benchmarks to ensure product quality and safety. Partnerships with original equipment manufacturers (OEMs) require stringent quality control measures at every stage of production, reflecting the high level of accountability and dependability expected in automotive applications.
Furthermore, trustworthiness is a critical component in the relationship between plastic injection molders and automotive manufacturers. Trust is built through consistent performance, delivering parts that not only meet but often exceed clients' expectations. This trust is evidenced by long-standing collaborations with industry leaders, where plastic injection molders directly contribute to the innovation and advancement of automotive technologies. Transparency in operations, coupled with a commitment to sustainability through practices such as recycling and energy-efficient production techniques, also strengthens this trust.
In conclusion,
the role of plastic injection molding in the automotive industry is pivotal. Through real-world experience, expertise in innovative materials and techniques, authoritative adherence to standards, and fostering trustworthy relationships, this technology continues to drive the sector forward. Automotive manufacturers leveraging this process can expect to see enhanced product quality, faster production cycles, and ultimately, greater satisfaction for the ever-evolving demands of the consumer. Embracing this method not only solidifies a competitive edge in the industry but also aligns with the global shift towards sustainable and efficient manufacturing practices.