Ống định hình đặc biệt kéo nguội
2 月 . 16, 2025 08:30

Cold-drawn special shaping tubes, known in Vietnamese as Ống định hình đặc biệt kéo nguội, have reshaped various industries by offering unparalleled precision and strength in manufacturing processes. These tubes, crafted meticulously through a cold-drawing process, exhibit optimal dimensional accuracy, enhanced surface finish, and superior mechanical properties, making them indispensable across automotive, aerospace, construction, and heavy industrial sectors.
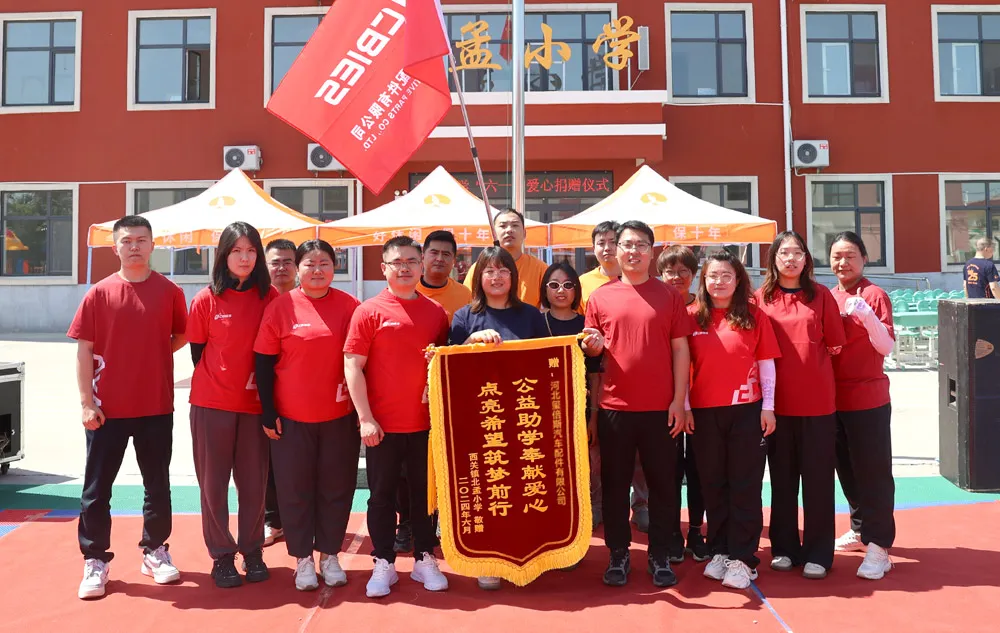
The cold-drawing process involves pulling the metal through a die without applying heat. This method not only improves the material’s surface finish but also aligns the grain structure, leading to heightened mechanical characteristics and superior tolerance control. Cold-drawn special shaping tubes offer the confidence of consistency, which is why industries with critical performance standards prefer these products.
In the automotive industry, the use of cold-drawn tubes is prevalent for creating components that demand both form and function—such as drive shafts, steering systems, and suspension components. These applications benefit from the tubes' exceptional strength-to-weight ratio, significantly impacting fuel efficiency and vehicle performance. By employing these tubes, manufacturers can enhance the vehicle's durability and reliability while maintaining design flexibility, allowing for lighter vehicle parts without compromising safety or integrity.
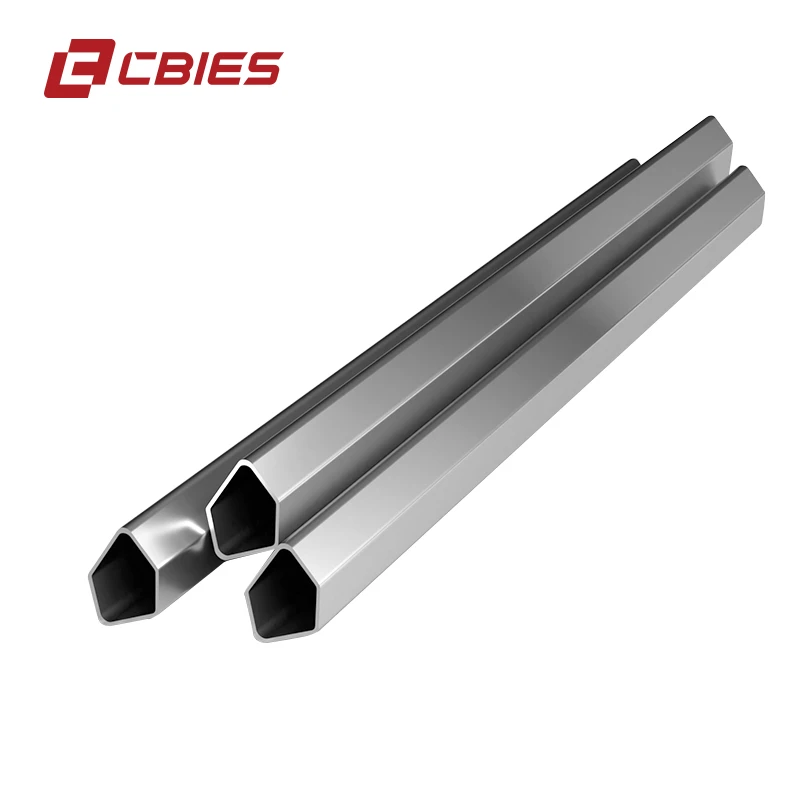
Aerospace manufacturers prioritize materials that can withstand extreme conditions.
Cold-drawn special shaping tubes fit this criterion perfectly. The meticulous production process ensures that the tubes can endure high-stress environments, offering dependable performance at high altitudes and various temperature ranges. Additionally, these tubes assist in achieving precise fittings and reduced weight, directly enhancing fuel efficiency and payload capacity of both commercial and military aircraft.
Construction and heavy engineering sectors leverage the precision and customization possibilities offered by these tubes. From structural supports to intricate architectural elements, the strength and adaptability of cold-drawn shaping tubes translate into buildings and machinery that perform reliably while adhering to strict compliance standards. Given their corrosion-resistant nature, they are also ideal for sustainable construction practices, reducing maintenance costs and promoting longevity.
Cold drawn special formed tubes
Expert insights reveal that the adoption of cold-drawn special shaping tubes is not merely beneficial but essential for forward-thinking industrial advancements. Industry authorities emphasize that while initial investment might seem higher, the lifecycle benefits far outweigh upfront costs. The longevity, reliability, and performance contribute significantly to reducing overall operational expenses.
From a trust standpoint, choosing cold-drawn special shaping tubes also means aligning with certified manufacturing processes that emphasize quality control and material traceability. This level of integrity in production fosters not only confidence in performance but also compliance with international manufacturing standards.
In the evolving landscape of industrial manufacturing, the push towards more sustainable and efficient operations underscores the need for materials that enable innovation without compromising on safety or quality. Cold-drawn special shaping tubes deliver on these fronts, supporting industries in achieving more with less—less energy, less waste, and less environmental impact.
For companies seeking to edge out competitors and lead in their fields, investing in the right materials is paramount. Cold-drawn special shaping tubes represent an intersection of advanced technology and practical application, embodying a strategic choice that aligns with the future of industry benchmarks.
In summary, cold-drawn special shaping tubes offer unmatched advantages across multiple industries through their precision engineering, reliable performance, and adaptability to stringent requirements. These qualities not only enhance product offerings but also define an industrial standard that prioritizes sustainability, efficiency, and excellence. Businesses that incorporate these tubes into their manufacturing processes position themselves at the forefront of innovation, gaining a critical edge in a competitive global marketplace.