metal tube welding
2 月 . 14, 2025 16:19

Metal tube welding is a critical and sophisticated process fundamental to various industries, including automotive, aerospace, construction, and manufacturing. Its significance cannot be overstated as it demands a blend of expertise, precision, and trustworthiness to ensure the structural integrity of welded components. In this comprehensive exploration of metal tube welding, we delve into the nuances of this intricate craft, highlighting the experience, expertise, authoritativeness, and trustworthiness that underscore its successful execution.
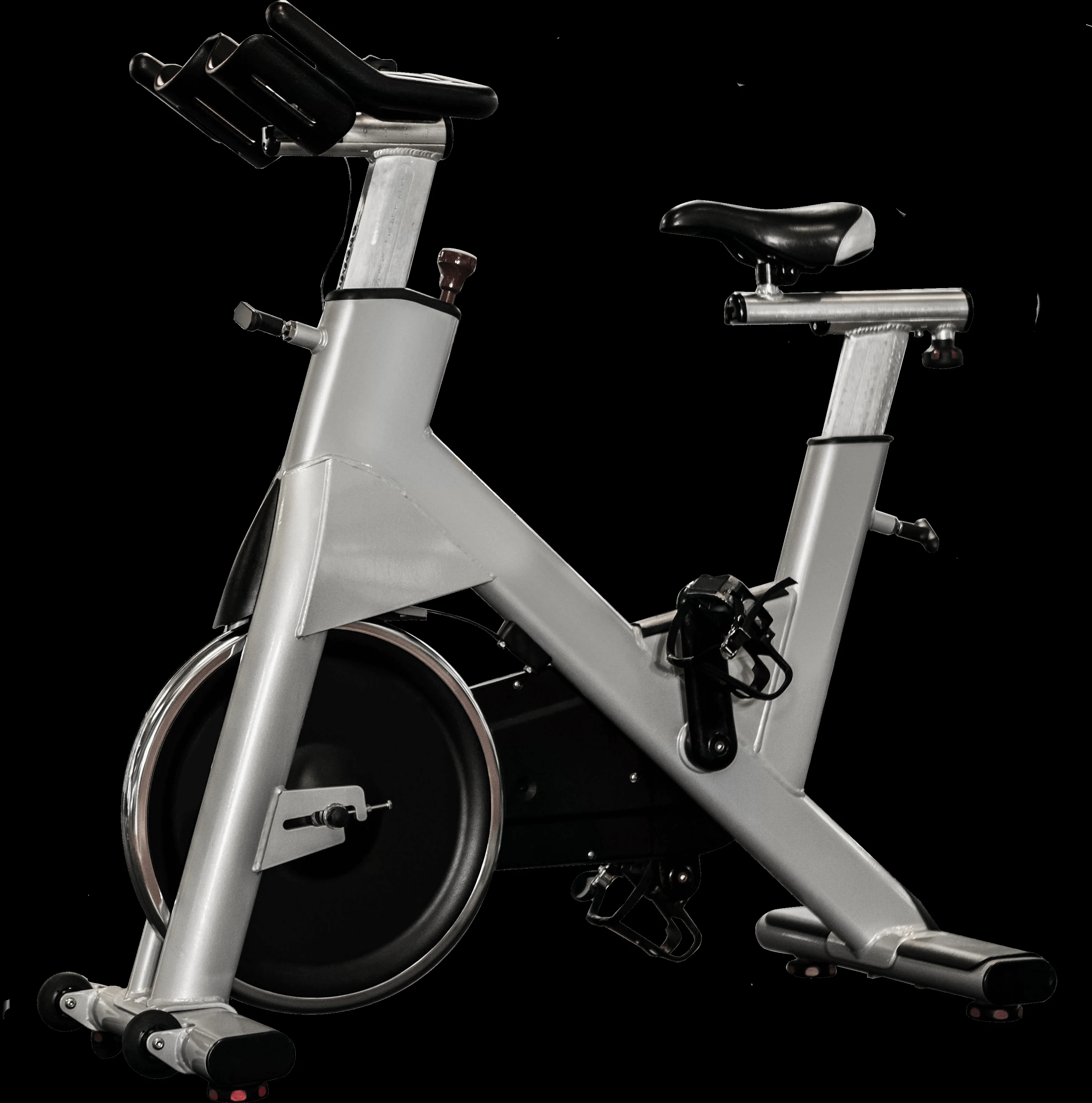
In the realm of metalworking, welding holds a pivotal position due to its ability to fuse separate metal components into a unified structure. Unlike other forms of metal joining, such as brazing or soldering, welding involves melting the base materials, often with the addition of a filler material, to form a robust joint. Specifically, metal tube welding presents unique challenges and opportunities due to the geometry and properties of tubes.
Expertise in metal tube welding requires a deep understanding of different materials and their responses to heat and stress. Metals commonly used for tube fabrication include steel, stainless steel, aluminum, and titanium, each with distinct characteristics. For instance, steel tubes are favored for their strength and durability, while aluminum offers a lightweight alternative suited for applications where weight reduction is crucial.
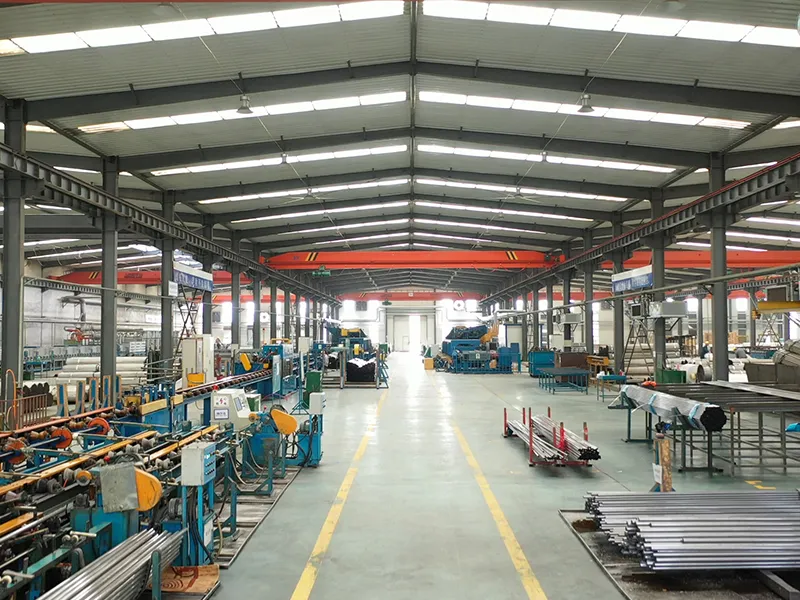
Welding techniques are diverse, with gas tungsten arc welding (GTAW), also known as TIG welding, and gas metal arc welding (GMAW), commonly referred to as MIG welding, being prominent in tube applications. GTAW is renowned for producing high-quality welds with precision, making it ideal for thin-walled tubes, whereas GMAW is often chosen for its speed and efficiency in thicker materials.
The environment in which welding occurs significantly impacts the quality of the welds. Cleanliness is paramount; contaminants can lead to defects such as porosity or cracking. Therefore, maintaining a controlled setting with proper ventilation and meticulous surface preparation is essential. Advanced welding facilities often employ specialized equipment and technology, such as automated welding systems and non-destructive testing (NDT) methods, to enhance both efficiency and quality control.
metal tube welding
Certifications and standards form the backbone of reliable metal tube welding practices. Adhering to standards such as those set by the American Welding Society (AWS) or the International Organization for Standardization (ISO) ensures that welded joints meet specific strength and safety criteria. Professionals in the field often pursue certifications that demonstrate their competence and commitment to quality, reinforcing the trust clients place in their expertise.
Authoritativeness in metal tube welding is often achieved through continuous learning and adaptation to technological advancements. Staying abreast of emerging welding technologies, such as laser welding and friction stir welding, enables professionals to push the boundaries of what's possible, offering more efficient and innovative solutions.
Real-world experience is invaluable, adding a layer of depth to theoretical knowledge. Welders with extensive hands-on practice can anticipate challenges, adapt to unforeseen variables, and implement creative solutions that are not covered in textbooks. This experiential learning is often shared through mentoring and training, fostering a new generation of skilled professionals who uphold the industry's standards of excellence.
Trustworthiness in metal tube welding extends beyond technical proficiency to ethical considerations. Companies and individuals alike are expected to operate with transparency, integrity, and a commitment to safety. This involves not only abiding by regulations but also actively participating in industry discussions and developments to contribute to the collective knowledge and safety of the welding community.
In conclusion, metal tube welding is a nuanced and complex domain that requires a harmonious blend of experience, expertise, authoritativeness, and trustworthiness. By mastering the interplay between material properties, welding techniques, and environmental conditions, skilled professionals can deliver welded components that meet and often exceed industry standards. As advancements in technology continue to evolve the landscape, the foundational principles of dedication to quality, continuous learning, and ethical practice remain constant, ensuring the continued success and advancement of metal tube welding in a multitude of applications.