hot finished welded tubes
2 月 . 14, 2025 15:48
Hot finished welded tubes, a staple in various industrial applications, stand as a testament to precision engineering and manufacturing excellence. Unlike their cold-formed counterparts, these tubes undergo a thermal process that bestows them with unparalleled durability and robustness, making them ideal for high-stress environments including construction, automotive, and energy sectors. Through years of progressive enhancements and technological advancements, hot finished welded tubes are now synonymous with strength and reliability.

In the realm of industrial manufacturing, the significance of hot finished welded tubes cannot be understated. Their fabrication process involves welding metal strips, followed by heating to a temperature that alleviates any internal stresses, ensuring a seamless and consistent structure. This process eliminates any potential anomalies that could compromise the tube's integrity under pressure, bolstering their application in demanding scenarios.
From an experiential standpoint, industries that have integrated hot finished welded tubes into their operations consistently report reductions in maintenance costs and downtimes. These tubes exhibit superior machinability, enabling industries to tailor them to precise specifications without losing structural integrity. Contractors and engineers, who prioritize quality and longevity, often favor these tubes due to their ability to withstand external pressures and high temperatures.
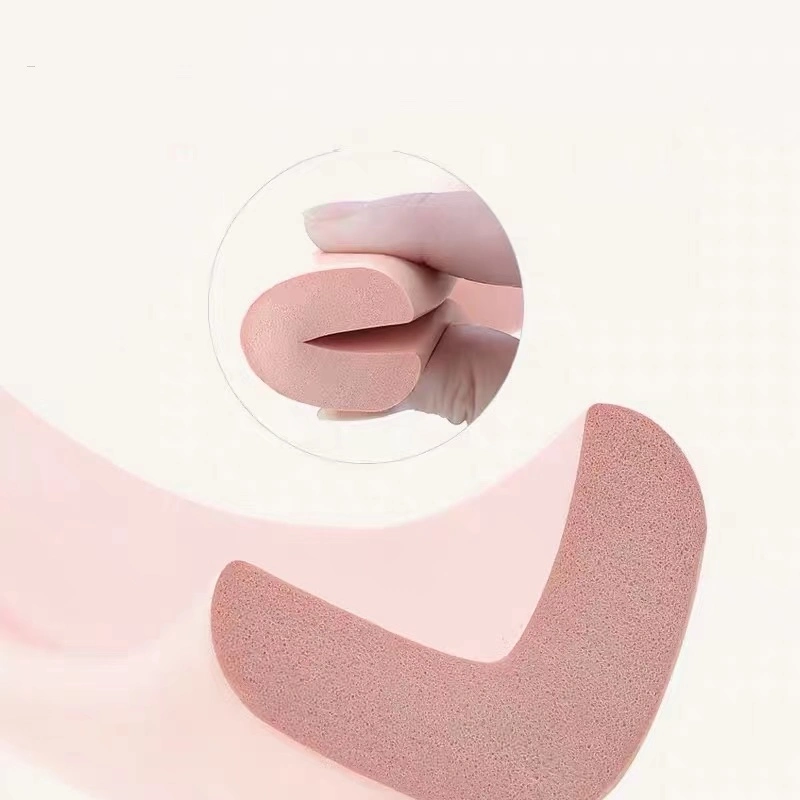
Expertise in the production of hot finished welded tubes involves a deep understanding of metallurgical properties and precise control over the heating process. Metallurgists and engineers collaborate to fine-tune the characteristics of the tubes, ensuring they meet stringent industry standards. This collaboration results in a product that's not only strong but also adaptable to various industrial needs, from thick-walled variants for robust applications to thinner, more flexible versions for intricate systems.
hot finished welded tubes
The authority of hot finished welded tubes in the market is further reinforced by international standards and certifications that attest to their quality. Organizations like ASTM and ISO provide rigorous benchmarks that reputable manufacturers adhere to, ensuring every tube delivers on its promise of performance and reliability. Selecting tubes that meet these globally recognized standards ensures that clients receive a product with proven efficacy, reducing the risk of failure in critical installations.
Trustworthiness, a crucial metric in evaluating industrial products, is inherently high for hot finished welded tubes due to the transparency and traceability of their production process. Reputable manufacturers provide comprehensive documentation detailing the manufacturing process, material composition, and compliance with relevant standards. This transparency fosters trust among clients, reassuring them that the product is both ethically and sustainably produced, aligning with modern demands for environmentally friendly manufacturing practices.
Leveraging the insights of experienced professionals, companies employing hot finished welded tubes benefit from expert guidance in application and maintenance, maximizing the longevity and performance of the tubes. This holistic support not only enhances operational efficiency but also educates users on best practices, further establishing the tube’s position as a critical component in industrial applications.
Ultimately, the ongoing innovation in hot finished welded tube manufacturing, coupled with a steadfast commitment to quality and reliability, ensures these components remain at the forefront of industrial solutions. Their unmatched strength, flexibility, and durability underscore their indispensability in sectors that demand uncompromising performance. As industries evolve, the adaptability and trusted performance of hot finished welded tubes will continue to play a pivotal role in driving technological and infrastructural advancements.