electric welded tube
2 月 . 14, 2025 13:53

Electric welded tubes have become essential components in various industries, from construction to automotive manufacturing, owing to their versatility, durability, and cost-effectiveness. These tubes, crafted through a process of meticulously welding electrical resistance and fusion, offer consistent quality that caters to high-demand applications. With fabrication involving precision-controlled procedures, the expertise required in producing these tubes is undeniably critical.
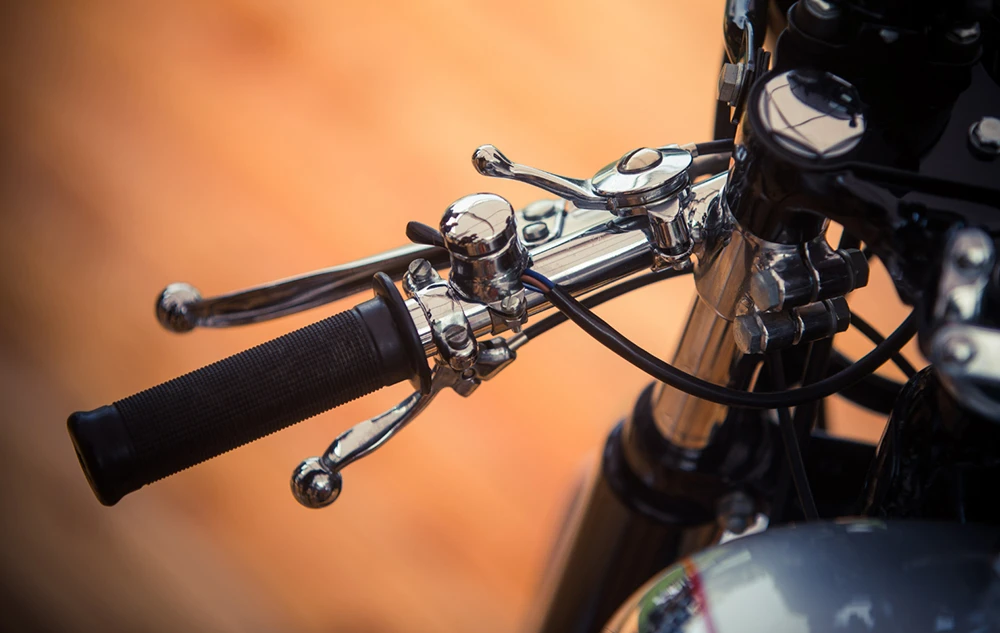
In construction, the adaptability of electric welded tubes cannot be overstated. Architects and engineers prefer these tubes because they provide a robust framework for buildings and structures. Their ability to withstand significant stress and environmental influences makes them an attractive option for creating dependable structural supports. Moreover, electric welded tubes' seamless appearance and available variations in thickness allow customization to meet specific project requirements, further showcasing their role in modern architectural designs.
Moving into the automotive sector, electric welded tubes play a pivotal role. Their high tensile strength and unique ability to be molded into various shapes make them indispensable in manufacturing lightweight yet durable vehicle parts. Using these tubes contributes to weight reduction in vehicles, which directly impacts fuel efficiency and performance, addressing both environmental concerns and consumer demands for cost-effective transportation options. The expertise involved in producing these high-performance components guarantees that each tube adheres to stringent automotive industry standards, ensuring safety and reliability.
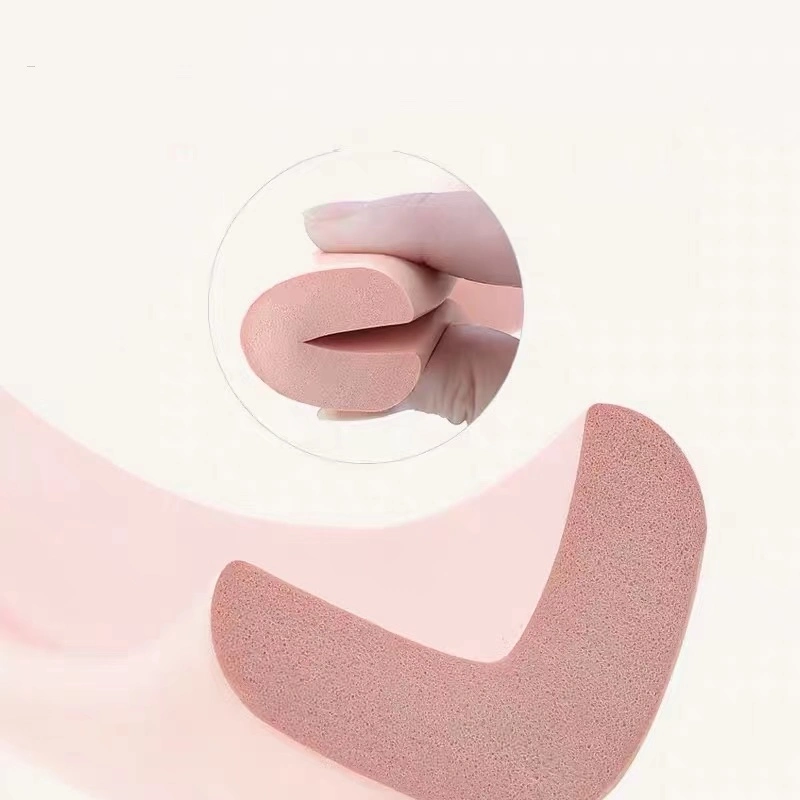
Another critical domain where these tubes make a significant impact is the manufacturing industry. Their precise engineering ensures uniformity and consistency, which are crucial for manufacturing processes that require exact specifications. Industries rely on electric welded tubes for producing everything from furniture to complex machinery parts. The trustworthiness of these tubes stems from rigorous quality control measures, which ensure that each product meets the industry's rigorous safety and performance criteria. This establishes them as highly authoritative in environments where precision is paramount.
electric welded tube
Trust plays an integral role in opting for electric welded tubes. Certified production processes and third-party verifications provide assurance that these tubes meet international standards and environmental regulations. Factories employing advanced technology and quality management systems instill confidence in consumers and businesses alike, making these tubes a reliable choice for environmentally sustainable, long-lasting, and efficient solutions.
In addition to their technical benefits, electric welded tubes present a sustainable choice for industries striving for responsible production. Using recycled materials in their manufacture diminishes environmental impact and positions companies as leaders in eco-friendly initiatives. This aspect resonates well with the E-A-T principles, aligning professional expertise and trust with ecological responsibility, a growing concern worldwide.
In conclusion, electric welded tubes epitomize a blend of sophistication, strength, and sustainability. Their applications across various industries underscore their versatility and the high level of expertise required in their production. By adhering to stringent quality standards and embracing environmentally sound practices, they serve trustworthiness and authority in industries striving for innovation and resilience. The continued evolution and optimization of production techniques hold promise for even wider adoption and efficacy, meeting the ever-changing demands of the modern industrial landscape.