electric resistance welded tube
2 月 . 14, 2025 13:06
Electric resistance welded (ERW) tubes offer a remarkable balance of strength, durability, and affordability, making them invaluable in numerous industrial applications. Manufactured through a process that involves cold-forming steel coils into a round cylinder and then employing electrical currents to weld the seam, ERW tubes are designed to provide a high-strength bond, suitable for handling both high pressure and load-bearing conditions. Given this unique manufacturing process, ERW tubes are differentiated in the market for their seamless, smooth finish and enhanced structural integrity.
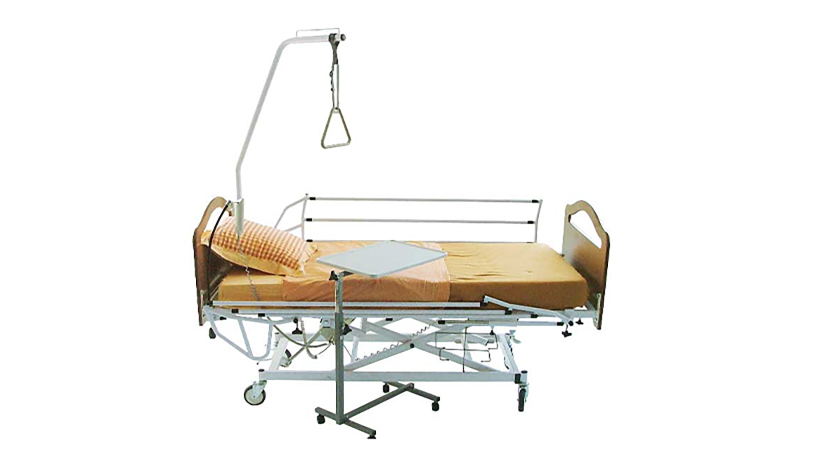
From a professional standpoint, the precision in the manufacturing process of ERW tubes ensures they meet stringent quality standards required in various sectors such as construction, automotive, and infrastructure development. These tubes are particularly appreciated for their consistency, as the welding process is automated and controlled electronically, reducing the risk of human error. This automation results in tubes with less variance from piece to piece, which is crucial in large-scale applications where uniformity is a key factor.
In the construction industry, ERW tubes are lauded for their versatility and robustness. They are extensively used in scaffolding, fencing, and framework applications. Engineers prefer ERW tubes because their welded joints are stronger when compared to other types of welded tubing, allowing for thinner walls in structural designs without compromising safety or performance. The strength of ERW tubes allows construction projects greater flexibility and scope for innovative design, facilitating the creation of both majestic skylines and functional infrastructure.
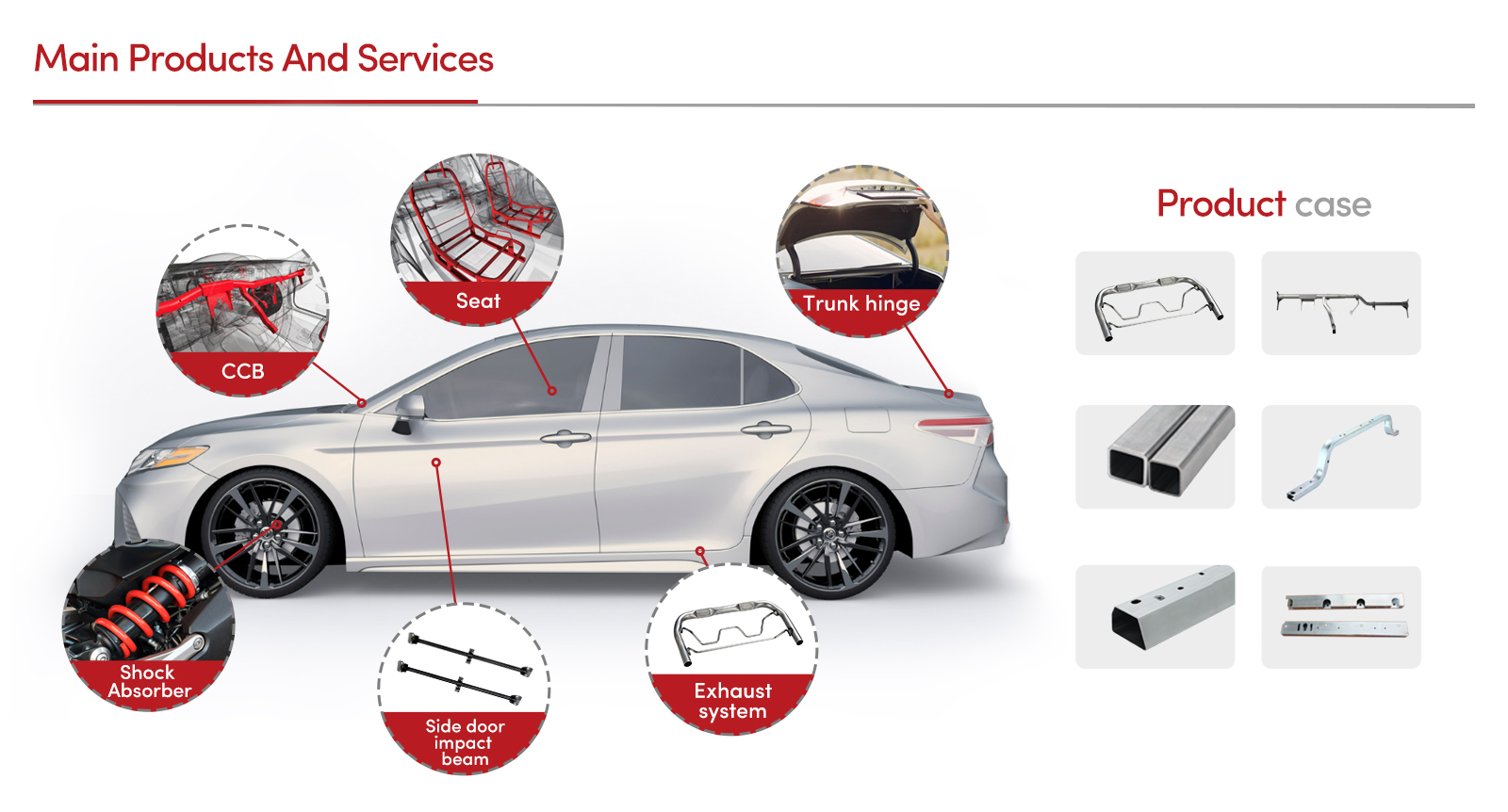
For those involved in automotive manufacturing, ERW tubes prove to be a critical component in building vehicles that require lightweight yet durable structures. Their usage spans across exhaust systems and roll cages to drive shafts and chassis, where material performance can directly influence vehicle safety and efficiency. Automation in ERW production means reduced material waste and more sustainable manufacturing practices, aligning with the growing call for environmentally conscious industrial processes.
electric resistance welded tube
Some consumers express concerns regarding the longevity of ERW tubes when exposed to elements such as moisture or chemicals. However, advances in protective coatings and galvanization techniques have significantly improved the tubes' resilience against rust and corrosion. Industry experts stress the importance of selecting the appropriate grade of ERW tube for the intended environment, as this can dramatically extend the lifespan and functionality of the product.
Experts in engineering and materials science often advocate for ERW tubes as the material of choice in both design and functionality. This endorsement speaks to the product's authority and reliability, which has been established through decades of use in challenging conditions worldwide. Moreover, regulatory bodies and standard organizations frequently reference ERW tubes in set engineering standards, underlying their integral role in safety and performance requirements across industries.
Trust in ERW tubes is further cemented by their adherence to international standards such as ASTM or ASME, which are benchmarks for quality in the metal tube manufacturing sector. Such certifications assure clients not only of the products’ mechanical properties but also of their compliance with environmental and safety considerations. The traceability in production, thanks to documented quality checks, enables a clear audit trail which is indispensable for maintaining trust and accountability in business-to-business transactions.
Overall, the narrative surrounding electric resistance welded tubes is one of reliability, versatility, and innovation. They empower industries to push boundaries while maintaining safety and efficiency—a testament to the seamless integration of technology and material science, promoting both progress and sustainability. These attributes when communicated effectively, ensure ERW tubes not only occupy a pivotal position in current industrial applications but also continue to shape future developments in construction, transportation, and beyond.