cold formed tube
2 月 . 11, 2025 23:39

Cold-formed tubes have been a game-changer in various industries, offering distinct advantages due to their unique manufacturing process. Unlike other tubing products that are created by traditional hot-forming methods, cold-formed tubes are shaped at room temperature, ensuring precision and strength, factors incredibly beneficial in structural applications.
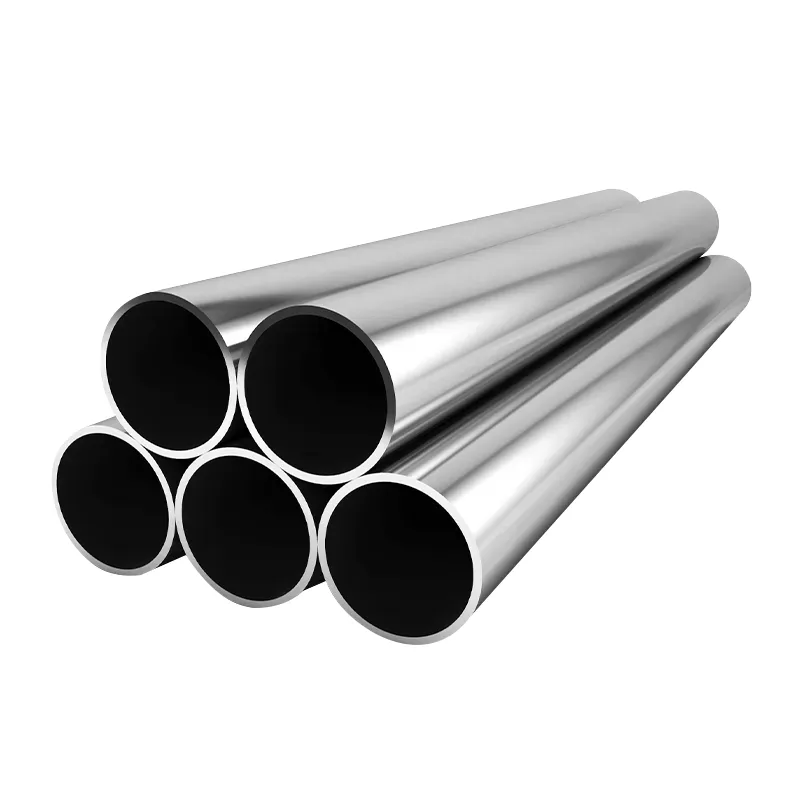
The precision associated with cold-formed tubes is rooted in their production process. During cold forming, sheets of metal are rolled to create tubes, while advanced techniques like computerized numerical control (CNC) provide unparalleled accuracy. This ensures minimal variations in the thickness and diameter, which is crucial for industries where precision is non-negotiable such as in the automotive, engineering, and construction sectors. In these fields, even the smallest deviation can lead to significant issues, making the reliability of cold-formed tubes indispensable.
In addition to precision,
cold-formed tubes boast exceptional strength. The cold-forming process improves the mechanical properties of the metal, enhancing its yield strength and hardness. These improvements arise because the process refines the tube’s grain structure, resulting in a product that can withstand greater loads and resist deformation under stress. This enhanced durability is particularly advantageous for structural engineering projects, where safety and longevity are of utmost importance.
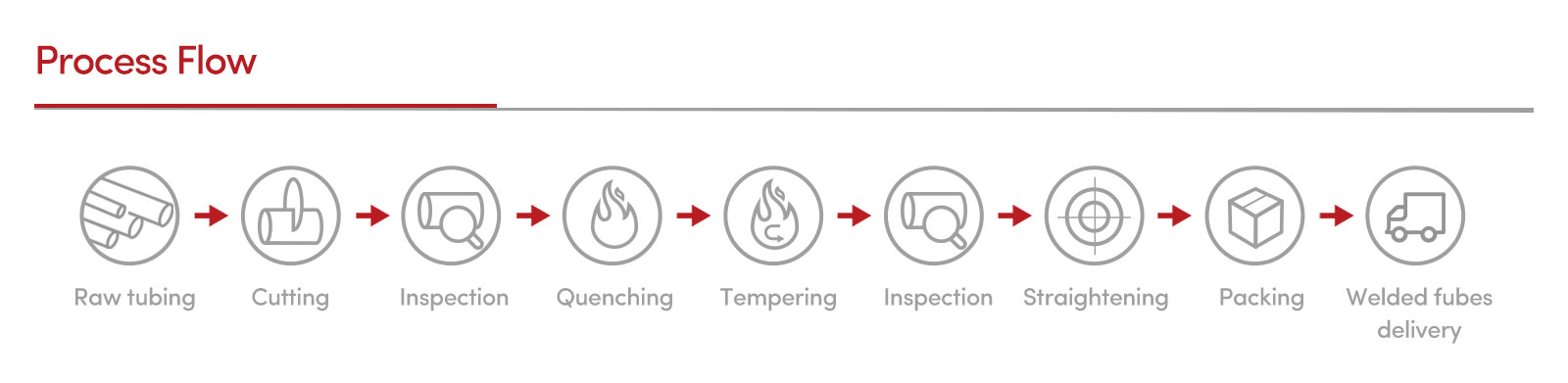
Moreover, the production of cold-formed tubes is cost-effective compared to their hot-formed counterparts. The process requires less energy, which translates into lower production costs. Additionally, the ability to produce these tubes to exact specifications reduces waste and maximizes efficiency, a crucial factor for manufacturers facing cost pressures. Therefore, companies seeking to maintain high quality while reducing expenses often turn to cold-formed tubes as a reliable solution.
cold formed tube
Sustainability is another key advantage. As industries worldwide strive to minimize their environmental impact, cold-formed tubes offer an eco-friendly option. Their production process emits fewer pollutants and requires less energy, aligning with green initiatives and meeting stringent environmental regulations. Companies using these tubes not only benefit from the superior product but also gain a reputation for being environmentally conscious, a significant selling point in today's market.
One of the most compelling reasons to choose cold-formed tubes is their versatility. They come in various shapes and sizes, adaptable to an extensive range of applications from lightweight bicycle frames to heavy-duty bridge supports. This adaptability ensures that regardless of the project requirements, there is a cold-formed tube solution available. It is this flexibility that makes them an attractive choice for engineers and designers looking for innovative and efficient material options.
Confidence in the quality of cold-formed tubes is bolstered by authoritative testing and certification. They are subject to rigorous quality assurance measures and comply with international standards, adding an extra layer of trust for their users. The manufacturers of these tubes often possess decades of expertise, providing a wealth of knowledge and a strong reputation in the field, which further enhances their credibility.
In conclusion, cold-formed tubes represent a combination of precision, strength, cost-effectiveness, sustainability, and versatility. Their reliability, backed by rigorous standards and expert manufacturing processes, demonstrates why they are increasingly preferred across various industries. For anyone seeking a material that offers both performance and peace of mind, cold-formed tubes stand out as a product synonymous with quality and innovation.