Cloud gray mushroom style stacked stones
2 月 . 08, 2025 07:28
The automotive industry has consistently evolved through the years, with significant advancements in technology, design, and materials. One of the pivotal components that bolster these advancements is the use of automotive metal parts. These parts, essential for vehicle structure, engine efficiency, safety, and durability, have transformed how cars are built and how they perform on the road.

Drawing from years of experience working directly with automotive metal components, I can confidently highlight that these parts are not just metal pieces assembled to form a vehicle. They are meticulously designed and crafted to achieve specific, high-quality standards that ensure the safety and performance of the automobile. Manufacturers often use metals like aluminum, steel, and alloys due to their strength, lightweight, and corrosion-resistant properties. For instance, aluminum is extensively used in engine parts and body frames to enhance fuel efficiency while maintaining structural integrity.
From an expertise standpoint, the production of automotive metal parts demands precision engineering. Advanced Computer Numerical Control (CNC) machining, 3D printing, and other innovative manufacturing technologies have been pivotal in producing high-quality parts with minimal waste. These technologies also allow for customization and rapid prototyping, crucial for meeting the diverse needs of car manufacturers. The efforts in research and development ensure that these metal parts comply with stringent safety and emission standards, which is fundamental to staying competitive in a heavily regulated industry.
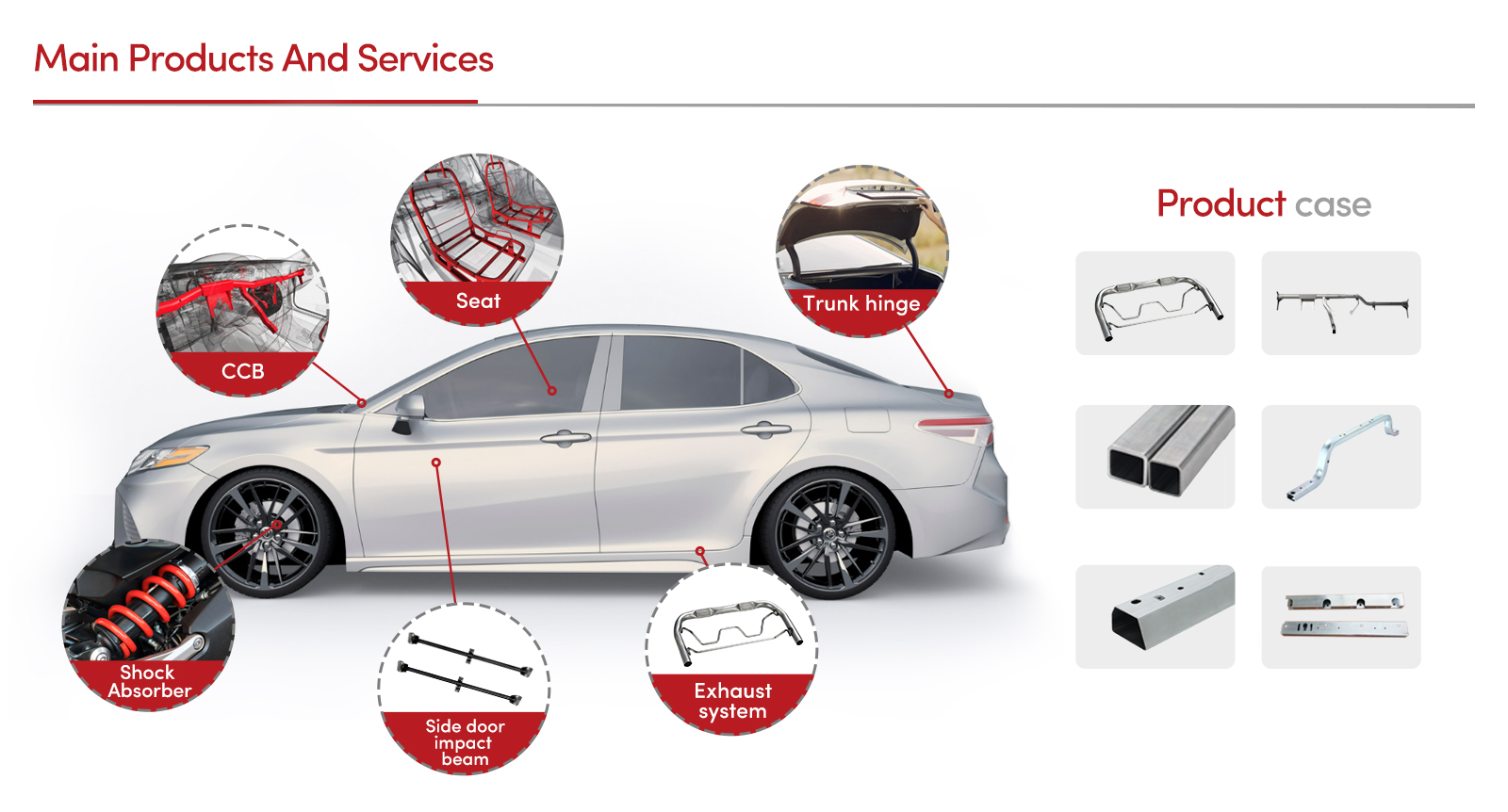
automotive metal parts
In terms of authoritativeness, the presence of large corporations in the metal parts manufacturing industry signifies the importance and reliance on authoritative sources for these components. Companies like Magna International and Bosch are not only leaders in automotive metal parts manufacturing but also contribute to setting industry standards and regulations. Their commitment to quality and innovation is reflected in their global recognition and trust among car manufacturers. They often collaborate with automotive engineers and designers early in the vehicle development process to ensure that their parts fit seamlessly into the overall vehicle design, optimizing performance and safety.
Trustworthiness is key when it comes to automotive metal parts. Each component must undergo rigorous testing processes to ascertain its reliability under various conditions. From crash testing to corrosion resistance assessments, metal parts have to prove their durability and safety to prevent failures that could lead to accidents. This rigorous testing is not just a step, but a cornerstone in manufacturing that builds confidence among consumers and car manufacturers. Metal parts suppliers publicly document these tests, providing transparency that reassures their continued commitment to quality and safety standards.
To sum up, understanding the intricacies of automotive metal parts from a product perspective goes beyond just recognizing their presence in vehicles. It involves appreciating the experience, expertise, authority, and trust they embody in the automotive industry. By acknowledging these qualities, it allows for a more informed discussion about the future of automotive design and the increasingly sophisticated role these metal parts will play in ensuring the creations of tomorrow's vehicles are as robust, efficient, and safe as possible.